ASSEMBLY TREE
The Assembly Tree displays data according to levels of installation or levels of belonging. Each lower-level item is installed on or belongs to the item immediately above it.
Figure 1 illustrates this approach to data control with an example of the components that make up the Base assembly.
In the left-hand frame, the Assembly Tree displays assemblies (blue text) and individual items without subcomponents (black text). In most screens, there is a checkbox saying 'Show Assemblies Only' that can be used to switch between showing only assemblies or all installed components in the left-hand frame.
Clicking on an assembly item in the left-hand frame displays sub-assemblies of that item in the left-hand frame and a list of all items attached to that item (or located at that location) in the right-hand frame. As seen in Figure 1, the resulting list in the right-hand frame can be filtered by Item Type and by Inventory Type. When filtering by item type Inspection, the list can be filtered by Inspection Type. The list can also be filtered to "Include items in sub-locations / sub-assemblies".
The Company ‘assembly' lists all the Bases, as well as Dead, and External Repairs. Any parts with history cannot be deleted and will be found in Dead. External Repairs houses components that are under current warranty repair orders and have yet to return to inventory or be moved to Dead. When looking inside any Base, as in Figure 1, there are some common locations. ‘Internal Repair' contains affected parts of open internal repair job cards. ‘Issued for Maint.’ contains non-consumable parts issued but not yet installed. 'Staffing’ is intended for Employees and, by extension, Training Requirements. 'Inventory’ will typically hold consumables and components not otherwise installed that are available for install.
The Inventory location itself has several sub-locations. Internal Shipping is where parts are installed when in transit from one Base to another; upon receipt, the part is installed to its intended destination. Parts are moved to Return to Inventory when they are removed in Technical Records. Tool Crib is generally used to store tools that aren't allocated or under repair. Awaiting Repair and Quarantine are not used automatically by the functions of RAAS, but parts can be received into these locations if desired or if necessary. Any parts in these inventory sub-locations will not be considered available and, as such, will not appear in the Quick Find Availability box.
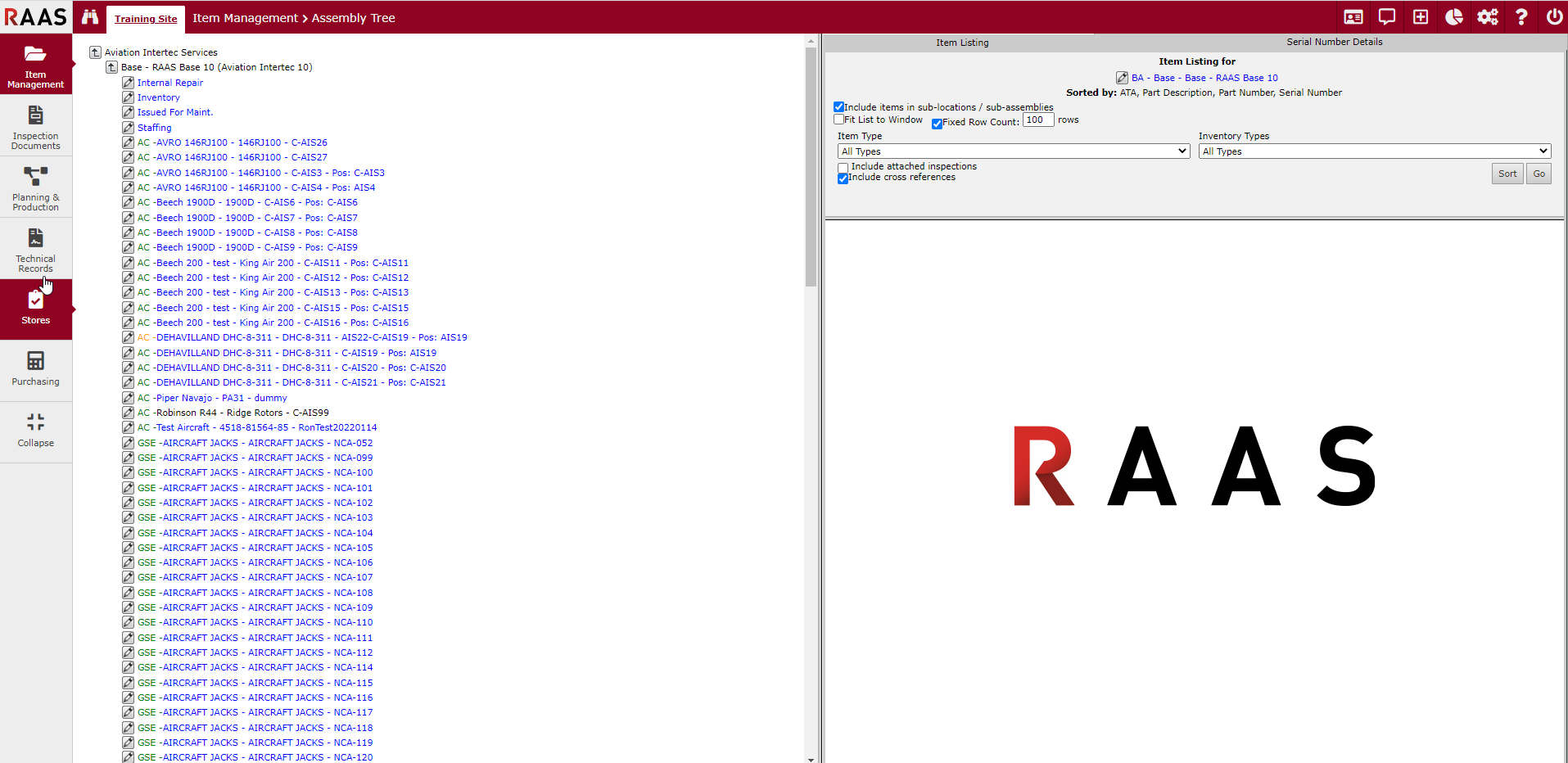
Figure 1 - Assembly Tree
When looking at the Serial Number Details tab, as in Figure 2 on the right-hand panel, you can see a selection's Installation and Location. The Installation is the immediate header the item is installed to, while the Location is the aircraft on which the item is installed or the location in which the item is located (e.g. a specific aircraft, Inventory, or a Base). The Installation and Location can be the same, though will not be in the case of sub-components.
Cross-reference (Cross Ref) information is now displayed at the part level in the Assembly Tree Item Listing and a view-only Cross Ref tab has been added to the serial number detail screen.
All items installed on an aircraft will be listed immediately below that aircraft in the Assembly Tree. All internal repair, inventory, issued for maint., staffing, aircraft, and ground equipment belonging to a base will be located below that base. All bases belonging to the company will be located below the company.
Within the Assembly Tree, only data associated with the part serial number can be viewed and changed. This is done by clicking the edit icon beside the item of interest.
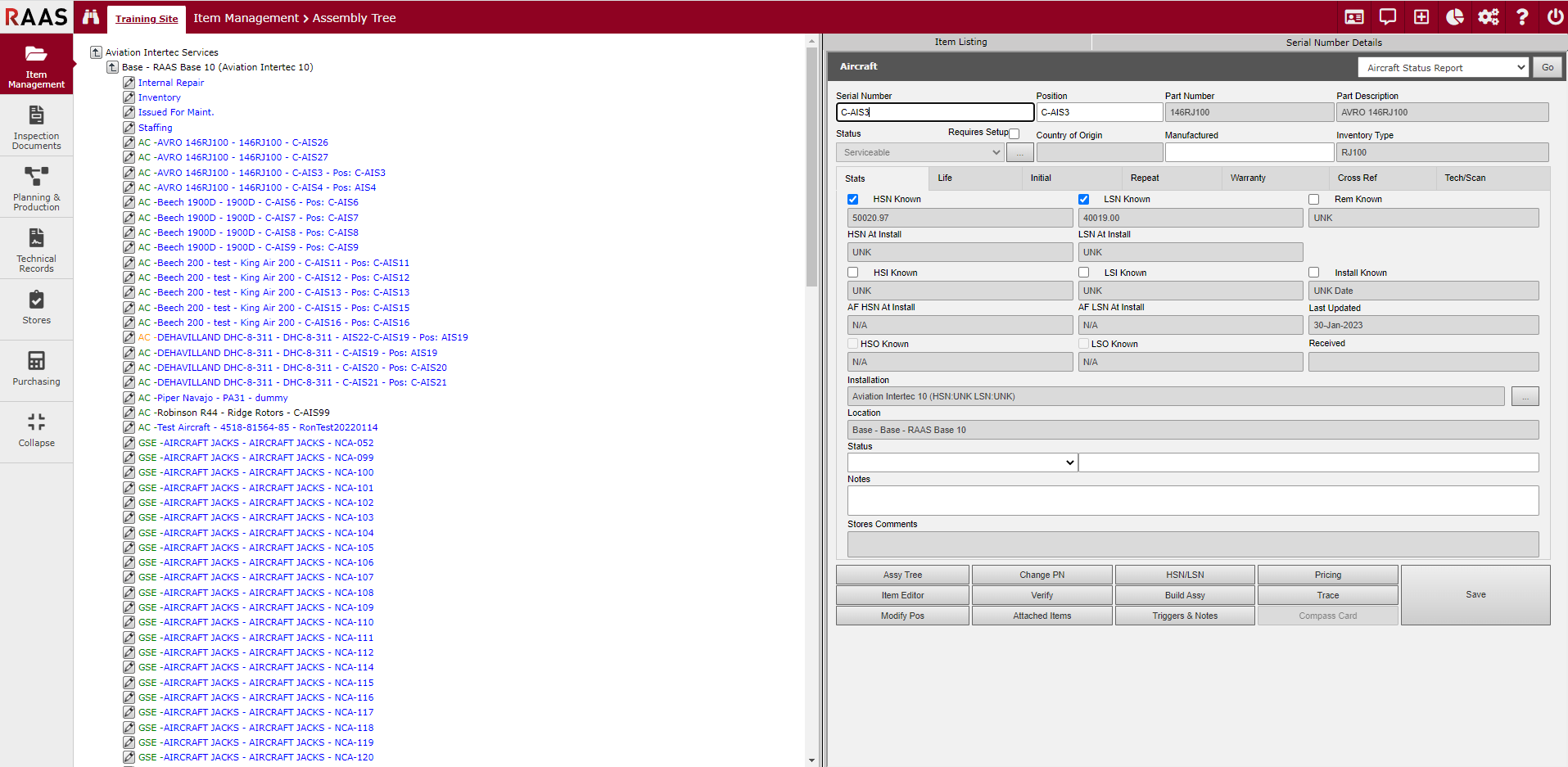
Figure 2 - SN Details