MATERIAL INSPECTIONS
A Material Inspection facilitates the approval of received parts and/or materials, enhancing traceability and ensuring compliance with required standards regarding their design and manufacture. When an Item is flagged “Material Inspection Required” at the Part Description level, it will appear in the Material Inspections List as “Pending Inspection” upon receipt. Parts cannot be installed on an aircraft via TMI Entry until the Material Inspection is completed and processed.
Navigation
Click Stores and select Material Inspections.
Figure 1: Material Inspections
Configuring Parts to Require a Material Inspection
At the Part Description level in Item Editor, click on the pencil icon.
Select “Requires Material Inspection”.
Save.
Note: Selecting “Send Notification on Receipt” will allow selected users to be notified when an item has been received.
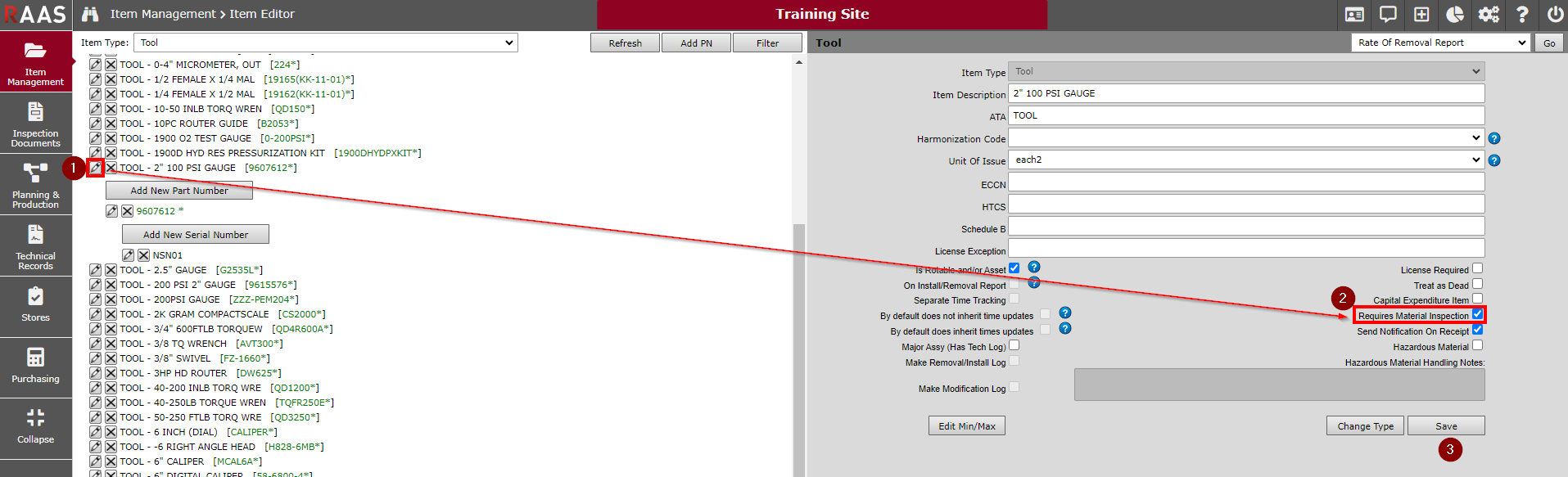
Figure 2: Set Up Requirements
Generating Report
Select the Received At location.
Select Inventory Type.
Choose a receipt date range or leave blank for all items.
Select filter options to view items that have passed inspection, are awaiting inspection, or have failed inspection.
Click Generate.
Select a Sort By option to change the sort order, if desired.
Figure 3: Material Inspections Report
Processing Material Inspections
Click Edit to complete the Material Inspection. (Click Delete to remove the item from the list.)
Select the Inspection Status from the dropdown menu.
Verify the Serviceability Status from the dropdown menu.
Enter Findings as of date.
Enter Inspection Notes.
Enter the User Password to sign off the Material Inspection.
Click Update Status.
Figure 4: Processing Material Inspections