JOB CARD PART REQUIREMENTS
In the dynamic landscape of aircraft maintenance, ensuring seamless coordination between tasks and required parts for job accomplishment is paramount for efficient operations. This document aims to provide clarity on how to effectively associate part requirements with Job Card Templates or MPD Tasks and describes the process by which these requirements translate into Job Card Part List items upon job issuance. This document further describes the automations available for Job Card Part List items by elaborating upon how Part Requests or Purchasing Inbox requests might automatically be created based on inventory status and configuration rules.
The Job Card Parts List will describe the part requirements for accomplishing a maintenance task. These Part List items can be associated to a Job Card in the following ways:
Job Card Templates
Parts can be added to the Part Requirements section of a Job Card Template. These parts will be automatically populated on the Job Card Part List when the Job Card is issued from the Maintenance Forecast should a corresponding JCT exist for that Aircraft Type, or when the template is imported into a Job Card.
Click Planning & Production and select Job Card Templates.
Select Generic or an Aircraft Type in the drop-down menu and click Go.
To add a Template see Job Card Templates.
Click the edit icon for the Template you wish to update.
Click Add in the Part Requirements section.
Note: Part Lists can also be Imported into the list from a .txt file by clicking the Import button.For Tracked Parts, search for the Part and click Find.
Note: Non-Tracked items can be added by removing the Tracked flag and entering a full Description.Add the Quantity required.
The Create Part Request from Job Card part list setting will suggest that a Part Request be created from the Job Cards Parts Requirement process action. If a Part Request is not required then this setting should be unchecked.
Click Save.
Icons will represent a Part (Tracked or Non-Tracked) vs a Tool.
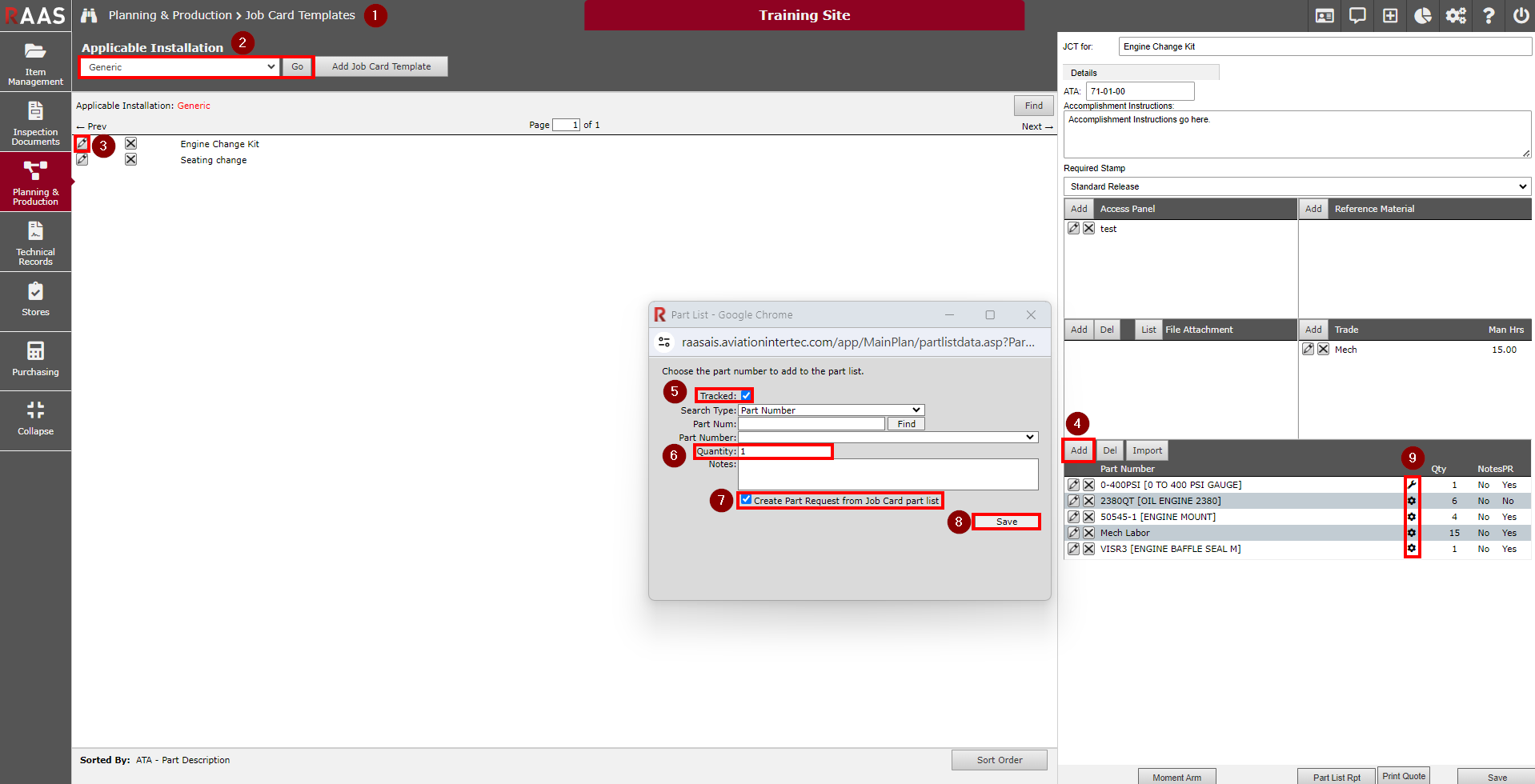
Figure 1: Adding Parts Requirements to Job Card Template
MPD Tasks
Parts can be added to the Parts Requirements section of an MPD task in Task Editor. These parts will be automatically populated on the Job Card Part List for aircraft that the task is applicable to when a Job Card is issued from the Maintenance Forecast with a corresponding JCT linked to the MPD task or when a JCT linked to the MPD task is imported into a Job Card.
Click Inspection Documents and select Task Editor.
Select a Task by clicking the left ellipsis.
Click Enter Revision Mode.
Click Add in the Part Requirements section.
For Tracked Parts search for the Part and click Find.
Note: Non-Tracked items can be added by removing the Tracked flag and entering a full Description.Add Quantity required.
The Create Part Request from Job Card part list setting will suggest that a Part Request be created from the Job Cards Parts Requirement process action. If a Part Request is not required then this setting should be unchecked.
Click Save.
Click Publish Changes.
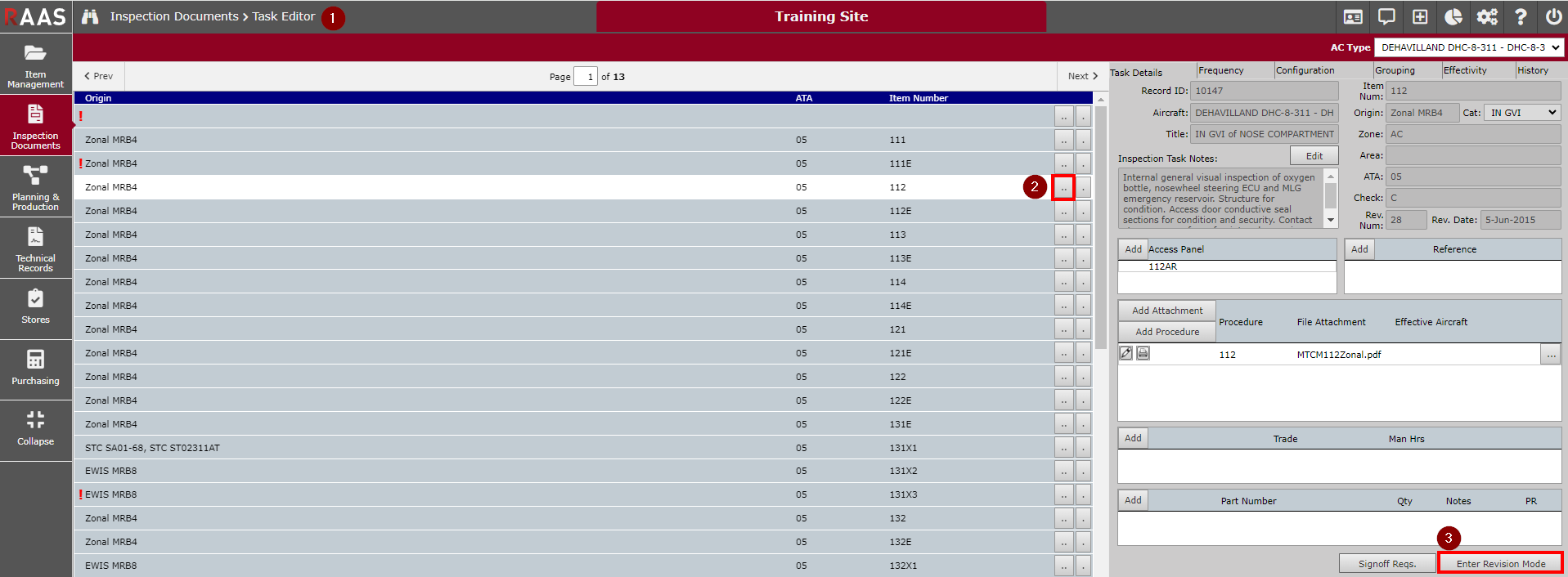
Figure 2: Adding Parts Requirements to MPD Task in IDM - Revision Mode (1-3)
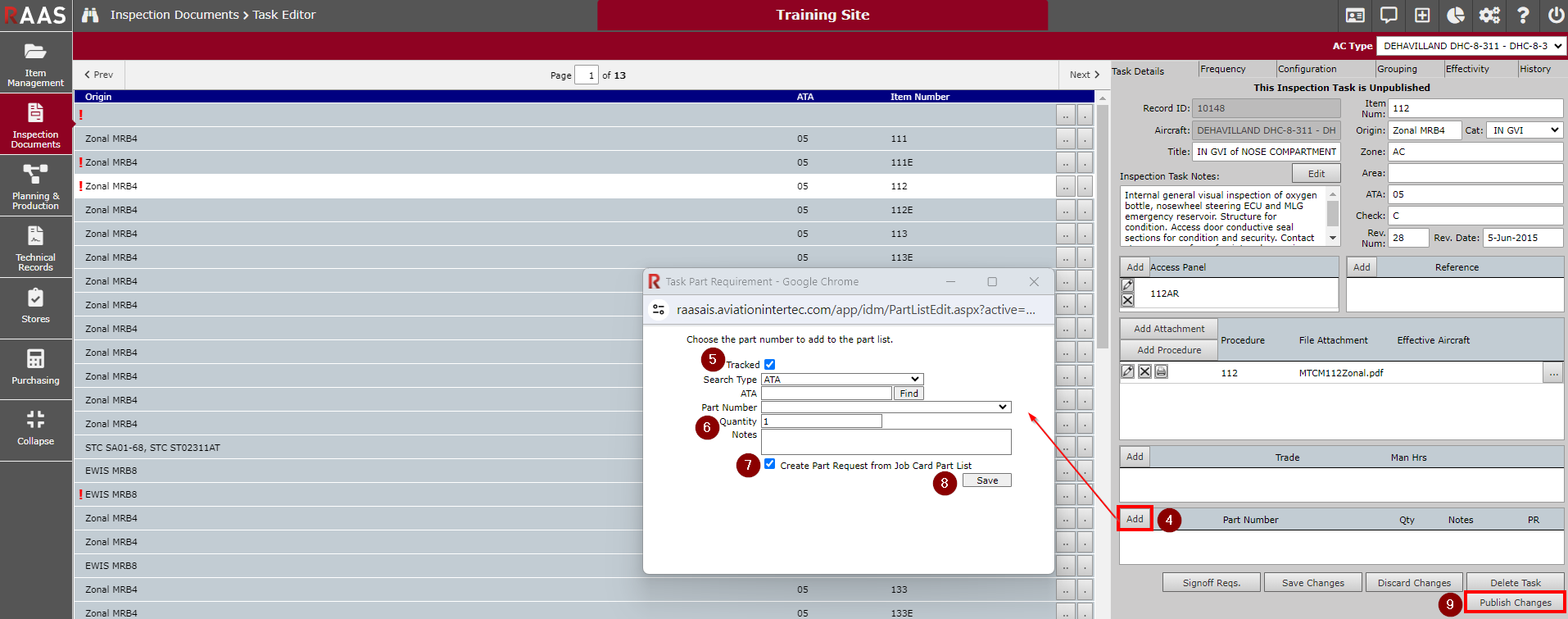
Figure 3: Adding Parts Requirements to MPD Task in IDM - Publish Changes (4-9)
Manually Adding Part Requirements to Job Card Part List
In the Job Card Detail screen, Parts Requirements can be manually added.
Go to Planning & Production > Job Card Listing or Stores > Job Card Listing.
Adding Parts to Part List
Go to the Part List tab.
Click Add.
For Tracked Parts search for the Part and click Find.
Note: Non-Tracked items can be added by removing the Tracked flag and entering a full Description.Add the Quantity required.
The Create PR setting will suggest that a Part Request be created from the Job Card Part List Process Items action. If a Part Request is not required then this setting should be unchecked.
Click Save.
Icons will represent a Part (Tracked or Non-Tracked) vs a Tool.
Note: These icons are color-coded to represent Material Availability (see color legend by clicking Material Avail.
icon).
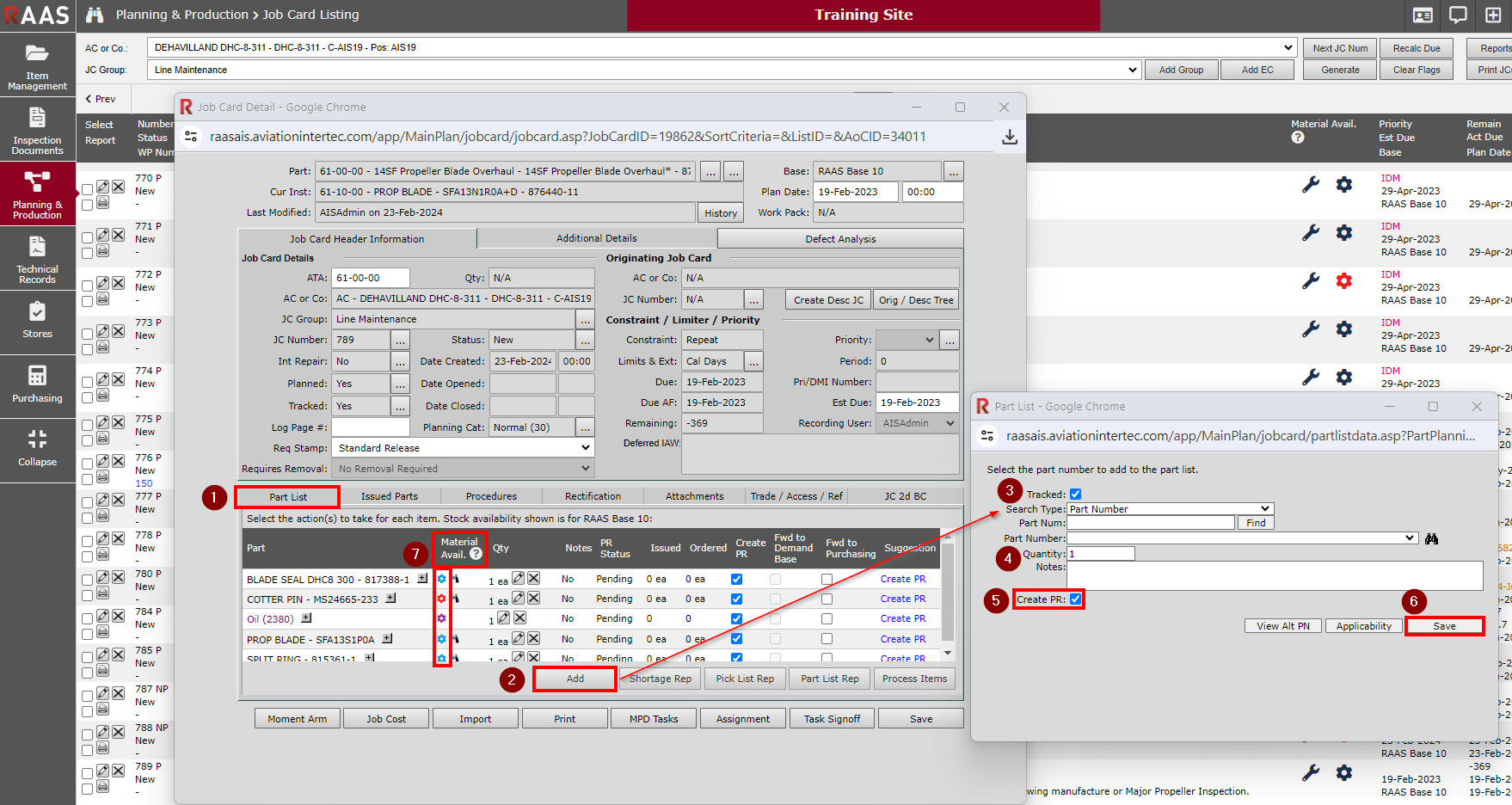
Figure 4: Adding Parts Requirements manually to a Job Card
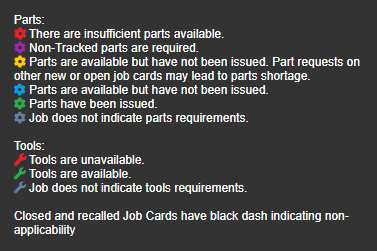
Figure 5: Material Availability Color Legend
Processing Part List Items
Part Requests are not automatically created when parts are added to the Part List of a Job Card. Depending on the inventory status at the Job Card Base of Maintenance, Base Information configuration settings, and Part Request demand base rules, RAAS will suggest actions to be taken.
When stock is available at the Job Card Base of Maintenance, if the flag to Create Part Request from Job Card part list for a given Part List item is set, RAAS will automatically suggest that a Part Request be created. When stock is not available at the Job Card Base of Maintenance, if the Job Card Base of Maintenance demands stock of another base, RAAS will additionally suggest forwarding the Part Request to the Demand Base when the Part List item is processed. If a Demand Base is not configured and the Job Card Base of Maintenance operates in an Open Stores environment, then RAAS will additionally suggest that a request to purchase additional stock is forwarded to the Purchasing Inbox when the Part List item is processed. The user is able to modify these suggestions as required.
When selecting the Process Items button, a new window will open which requests additional details for the newly created Part Requests (more details below).
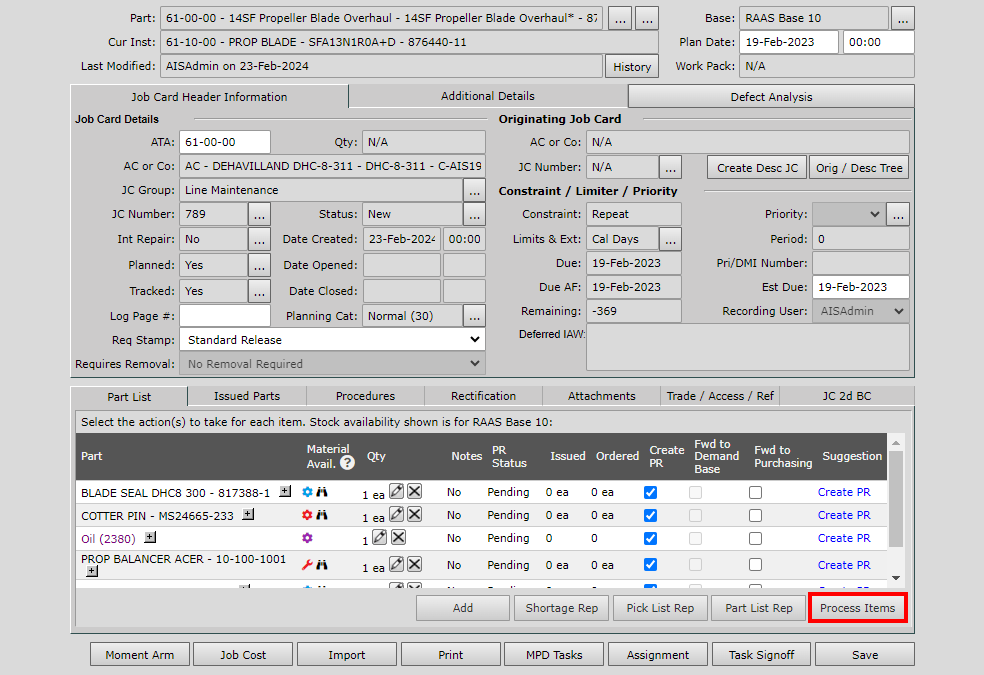
Figure 6: Sending Part Request to Stores
The Process Items window allows a user to set the time and date the Part Request is scheduled to be due. It also allows users to add the Part Request(s) to a Pick List by turning on the Pick Now flag and then also turning on the Add Part Request to a Pick List if stock is available flag*.
If the parts are to be picked later, the user would want to turn on the Pick Later flag instead.
If wanting to send a Part Request Notification to users subscribed to these notifications, turn on the Send Part Request Notification flag.
When satisfied with the selections, click Ok to process the items. A window will pop up informing the user that a Part Request was created along with the number of the Part Request. If the Pick Now and Add Part Request to a Pick List if stock is available flags were selected, it will also inform the user that a Pick List was created along with the number of the Pick List.
If the Pick Later flag was selected or the Add Part Request to a Pick List if stock is available flag was not selected, the Part Request(s) can be added to a Pick List later via the Part Request Listing or Part Request Detail screens as described on the Processing Part Requests help page.
Note that one of the Pick Later or Pick Now checkboxes must be selected to proceed with processing the items (a pop-up will notify the user if no selection is made).
*When users create new Part Requests from a Job Card, this setting will cause the Part Request user interface to suggest that the Part Requests be directly added to a material Pick List for immediate Pick List processing.
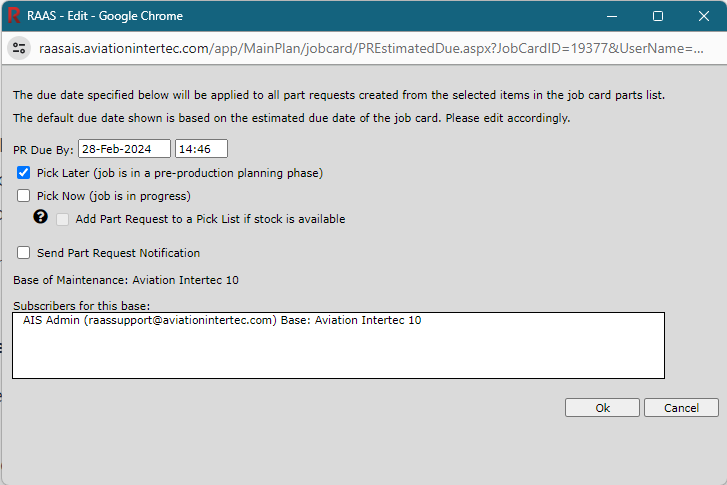
Figure 7: Process Items Window