JOB SCHEDULING ANALYSIS
Job Scheduling Analysis
The objective of Job Scheduling Analysis (JSA) is to provide visual identification of jobs that may be planned to be accomplished either too early or too late relative to the estimated due date and tolerance.
The module compares the planned date of a Job Card to the estimated due date of the Job Card. In the case of a Work Pack, the planned date of the Work Pack is compared to the estimated due dates of the Job Cards in the Work Pack.
Navigation
Planning & Production > Job Scheduling Analysis
Select Base and Aircraft to be graphed.
Select Period of 7, 14 or 30 Days to be graphed as well as the Plot Start Date, Plan Category and JC Types to be included (P/NP).
Utilization can be calculated by using Average, Detailed or an Imported Ops Schedule.
If an Ops Schedule is available then the module will visually identify conflicts between the Operational Schedule and the Maintenance Plan. Conflict types include, a) aircraft is scheduled to be flying when maintenance is scheduled, b) the maintenance window is too short to accommodate the duration of maintenance planned, and c) the aircraft is scheduled to be on the ground at a station/base different than where the maintenance has been scheduled.
Once all filters and parameters are selected, click Generate to populate the JSA plot.
Figure 1: JSA Filters/Parameters
Job Scheduling Analysis Plot
Aircraft information including, Type, Model (PN), MSN and current HSN/LSN including last date of update.
Clicking on the Model (PN) and MSN will allow the user to see and edit the Aircraft Information.
Hovering over “Prev JC” will show New or Open JCs with a Plan Date prior to the current JSA plot.
Utilization Bar shows hours and landing accumulated against the airframe for a point in time.
Last airframe update plotted to per-minute granularity when driven by Flight Logs.
Last airframe update plotted to per-day granularity when driven by TMI Update.
Last airframe update is set to the last chronological Flight Log or TMI Update.
Green up to the last airframe update, with hover showing “Current Airframe Time” text.
Gray from the last airframe update when utilization used, with hover showing hours and landings accumulated.
Orange when ops schedule used, but no schedule data available, with hover showing “No scheduled data for this period”.
also used for on-ground segment exceeding a certain threshold, which could be indicative of missing data.
Transparent / blank for segments with ops schedules
A Yellow Triangle represents pending items due, a number will appear if multiple items are due at the same time.
Hovering over the triangle shows the following information for each pending item:
Part information (ATA + PD + PN + SN)
Due values, Limit, Constraint.
Constraint Description.
Issue button which allows user to issue JCs directly from the JSA plot.
A Sphere represents Job Cards that have been issued where icon color will depend on position.
A number will appear on the icon if multiple Job Cards are due at the same time, and the “worst case” due will decide the icon color.
Hovering over the sphere with multiple Job Cards will show all Job Cards with their own color.
Due values are taken from JC not the Part.
A Square represents Work Packs where the “worst case” due will decide the icon color.
When there are multiple Job Cards in the Work Pack the “worst case” due will decide the icon color.
Hovering over the square will show all Job Cards in the Work Pack with their own color.
Icon colors
Bright green = Planned date before due but within pre-tolerance. (see Tolerances)
Dark green = Planned date before due but outside pre-tolerance. (see Tolerances)
Dark green = No tolerance defined at PN, and anywhere before due.
Orange = Extension applied.
Red = Planned date after due
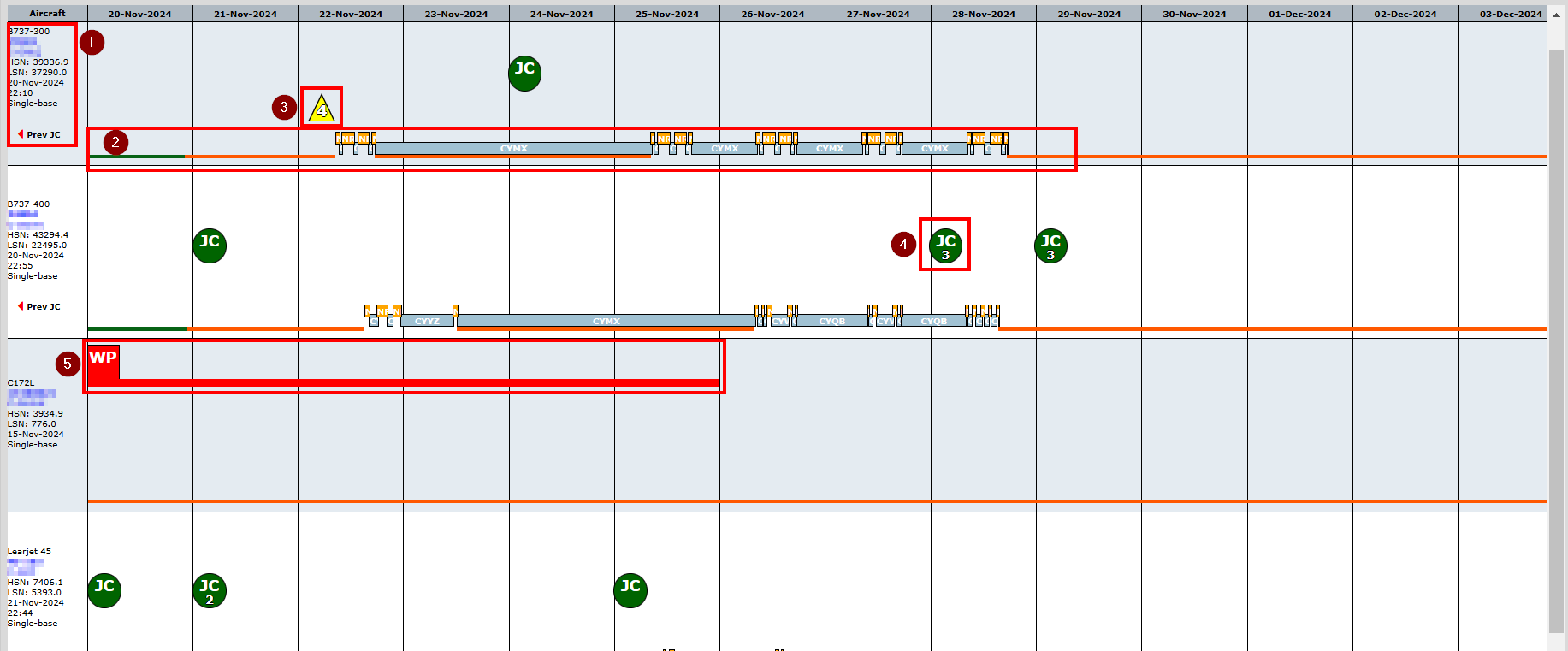
Figure 2: JSA Plot
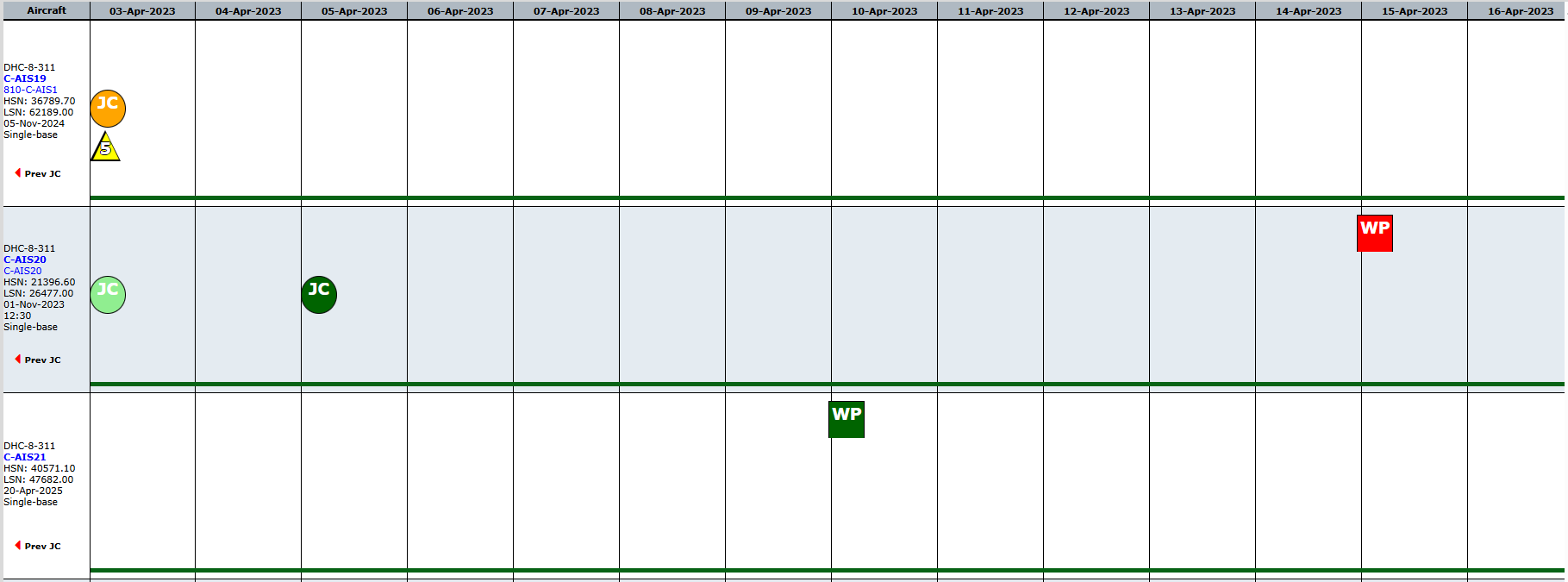
Figure 3: JSA Plot representing JC color codes
Tolerances
Job tolerances are also brought into the equation. If a tolerance exists for the constraint of a tracked Job Card then the module will use the utilization rates input to determine the tolerance lead and lag for a job, relative to the estimated due date. Using this information the module is able to identify jobs that may be planned to be accomplished too early relative to a calculated tolerance lead window as well as jobs that may be planned to be accomplished later than the estimated due date but within the calculated tolerance lag window.
Planning Categories
The Planning Category is used as a critical filtering criteria in the Job Scheduling Analysis planning utility, necessary to filter-out (exclude) maintenance jobs that are not mandatory. This is in recognition of the fact that when optional jobs are represented in a planning utility summary view like JSA then it can inadvertently cause the maintenance planner to place undue importance on non-mandatory jobs.
Manipulating the JSA Plot
Job Cards can be created (issued) or edited by hovering over the icon and selecting either ”Issue” or the existing JC number. Changes made to the Planned Date and Estimated Due of Job Cards will be reflected by regenerating the JSA plot as well as changing the Utilization rates.