MIN MAX REORDER
The Min Max Reorder screen allows users to view parts with Min/Max values set for each Inventory location and determine whether to reorder additional parts. This feature is designed to streamline your parts replenishment process by allowing you to easily generate multiple parts requests at once for items that fall below a predefined minimum stock level taking into consideration stock already on hand, on order, in transit, req for order, pre-allocated, and shelf expiring. RAAS will automatically suggest an Order Amount equal to the number needed to bring the quantity to the maximum value.
Setting Minimum and Maximum Stock Levels:
Before using the Min/Max Reorder module, it's essential to define the minimum and maximum stock thresholds for each inventory item. You can set these thresholds within the Part Description MIN MAX or can be reviewed based on your organization's usage patterns, lead times, and criticality of parts using MIN MAX SETTINGS.
Companies should ensure that these values are regularly reviewed and adjusted based on changing operational needs.
Navigation
Stores > Min Max Reorder
Select the Base inventory.
Filter for Item Type and Inventory Type, or leave as All Types to include all Inventory.
Enter Stock Expiry (days from today) to include the stock expiring variables.
Once the desired filters are selected, click Apply.
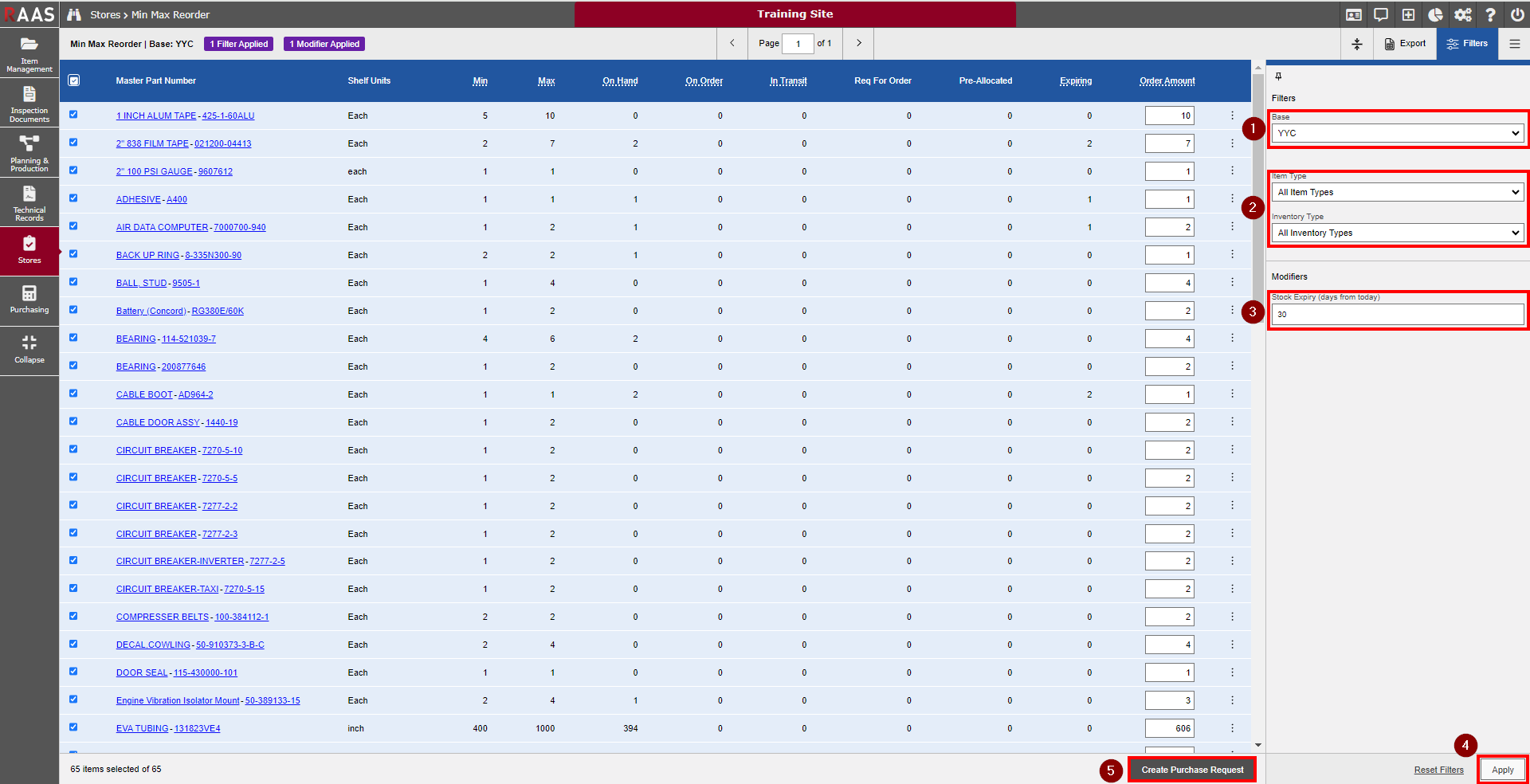
Figure 1: Min Max Reorder
The displayed results will include all Parts that have Min and Max values greater than 0 with a suggested Order Amount that is greater than 0 and will be sorted in alphabetical order by Part Description and then Part Number. Once the Order Amount reaches 0, the Part will be removed from the Listing as the purpose of Reordering is fulfilled. All items will be pre-selected to create a Part Request for the Suggested Order Amount.
The Suggested Order Amount value is calculated by the values of the following columns: Max, On Hand, On Order, Order Claims, In Transit, Restock Request, Expiring Stock.
Calculation: Order Amount = Max – On Hand – On Order + Order Claims – In Transit – Restock Request + Expiring Stock.
If there is no Expiring Stock, Order Amount = Max – On Hand – On Order + Order Claims – In Transit – Restock Request + 0.
Changes can be made as necessary by de-selecting parts, manually changing the order amounts and/or editing the Stock Expiry filter.
Once the order amounts are set for all applicable parts, click Create Purchase Request to create Part Requests for all selected parts.
Verify number of Purchase Requests being created, Estimated Due Date and click Confirm.
Part Request Estimated Due default value = Order Item ETA (days) + Today’s Date
Note: The Order Item ETA (days) can be defined in Company Settings.
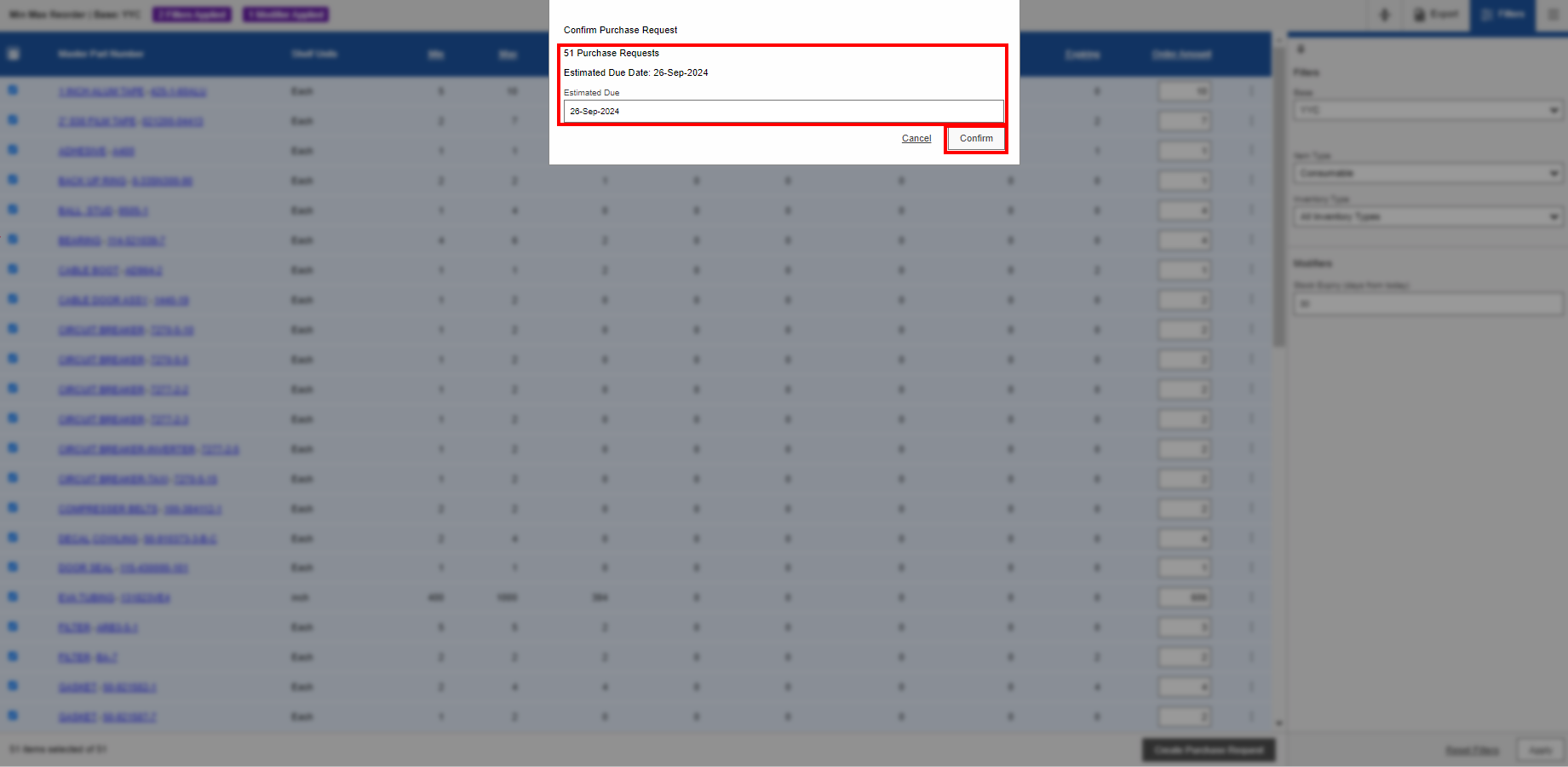
Figure 2: Creating Purchase Requests
The Purchase Requests will now be available to view in Stores > Part Requests Listing for processing.