MAINTENANCE DETAILS
Once the maintenance entry is in the TMI log, details may need to be added. Maintenance detail actions include: Install, Removal, Comply, Reset and Comply/Reset. The action may be Scheduled or Unscheduled. If Unscheduled, a problem must be selected. (Problems List can be found in Settings - Problems List). The problem, which indicates why the action is required, can range from warranty to failure.
Removal/Installation of a Part
Removal of a Part - Action, Reason, Problem
Click the Add New Detail button.
Select an Action, a Reason for the detail and the Problem that prompted the action.
Click Next.
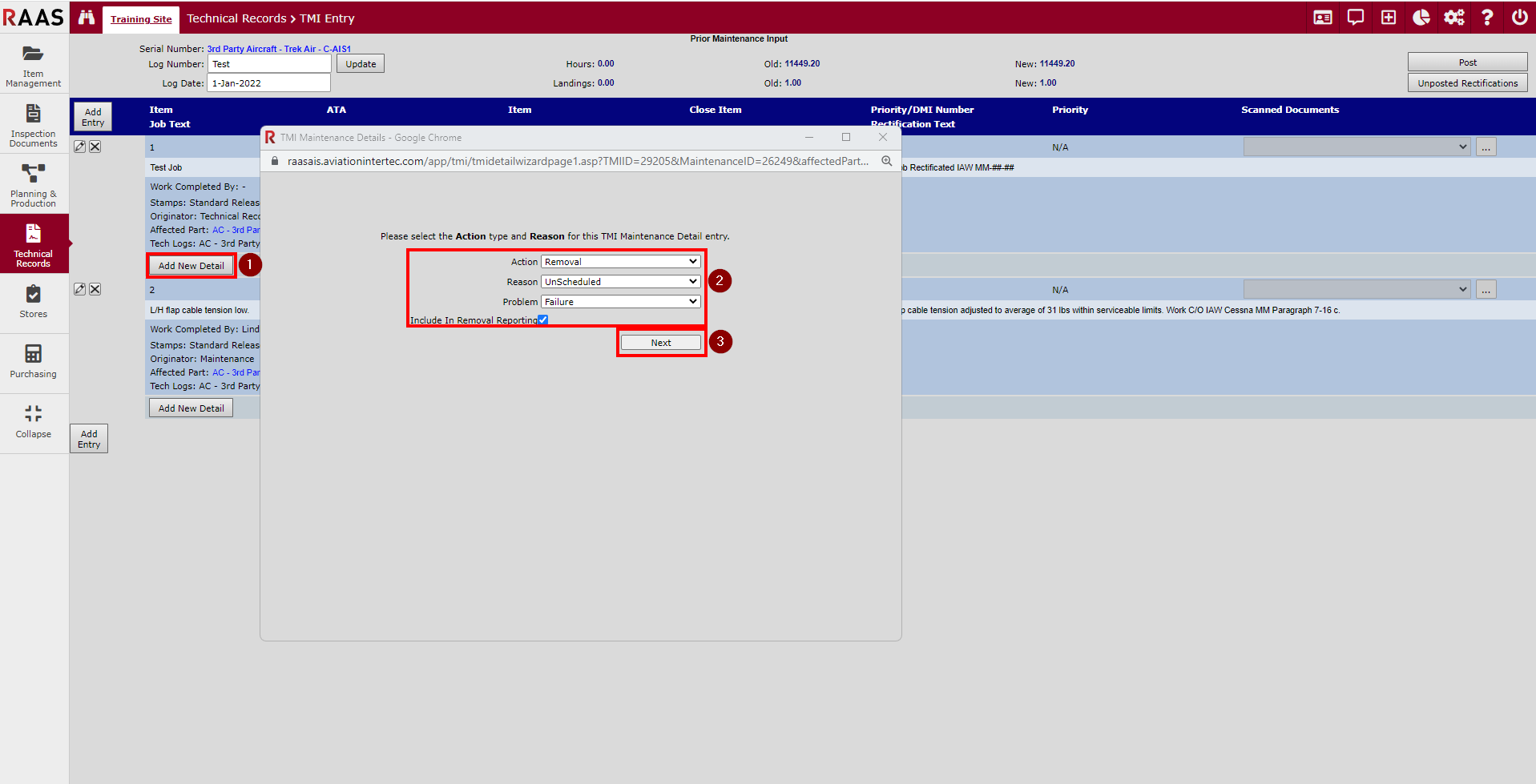
Figure 1: Action, Reason, Problem - Removal
The maintenance entry detail example in Figure 1 shows an item that is Unscheduled for Removal due to Failure.
Note: Scheduled Removals don’t necessarily require a Problem to be selected as they are assumed removed for Planned purposes.
Part for Maintenance
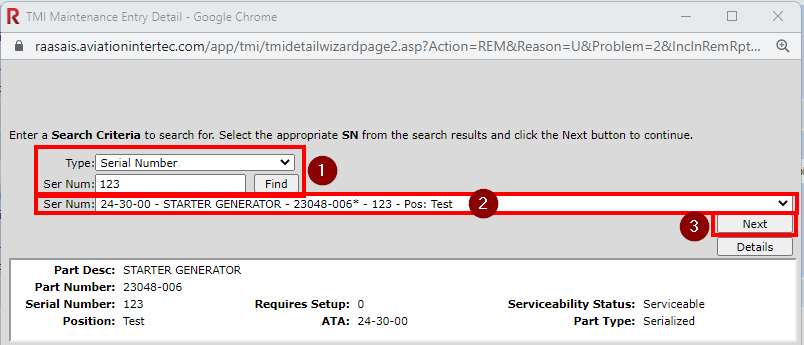
Figure 2: Selecting a Part to Remove
Base Selection
Select the Move To Base for removed parts.
Verify the Hours, Landings and Date.
Select the Serviceability Status at Removal for the selected part for maintenance.
Click Next.
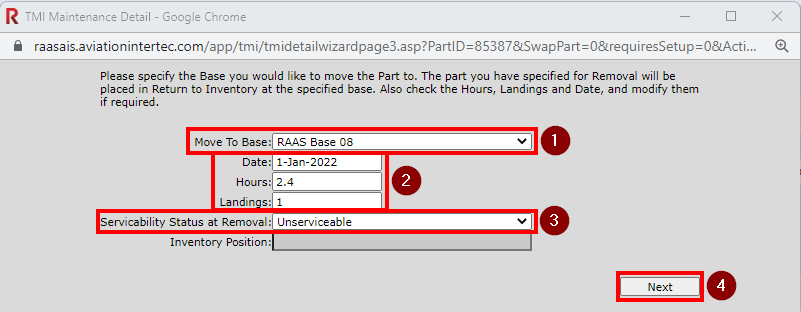
Figure 3: Configuration/Verification of Part Details at Removal
When performing a Removal action on a part, that part is placed in Return to Inventory at the specified Base.
Installation of a Part - Action, Reason, Problem
Click the Add New Detail button.
Select an Action, a Reason (Install Reason is normally Scheduled as part removal requires a new part install). No Problem is required for an Install.
Click Next.
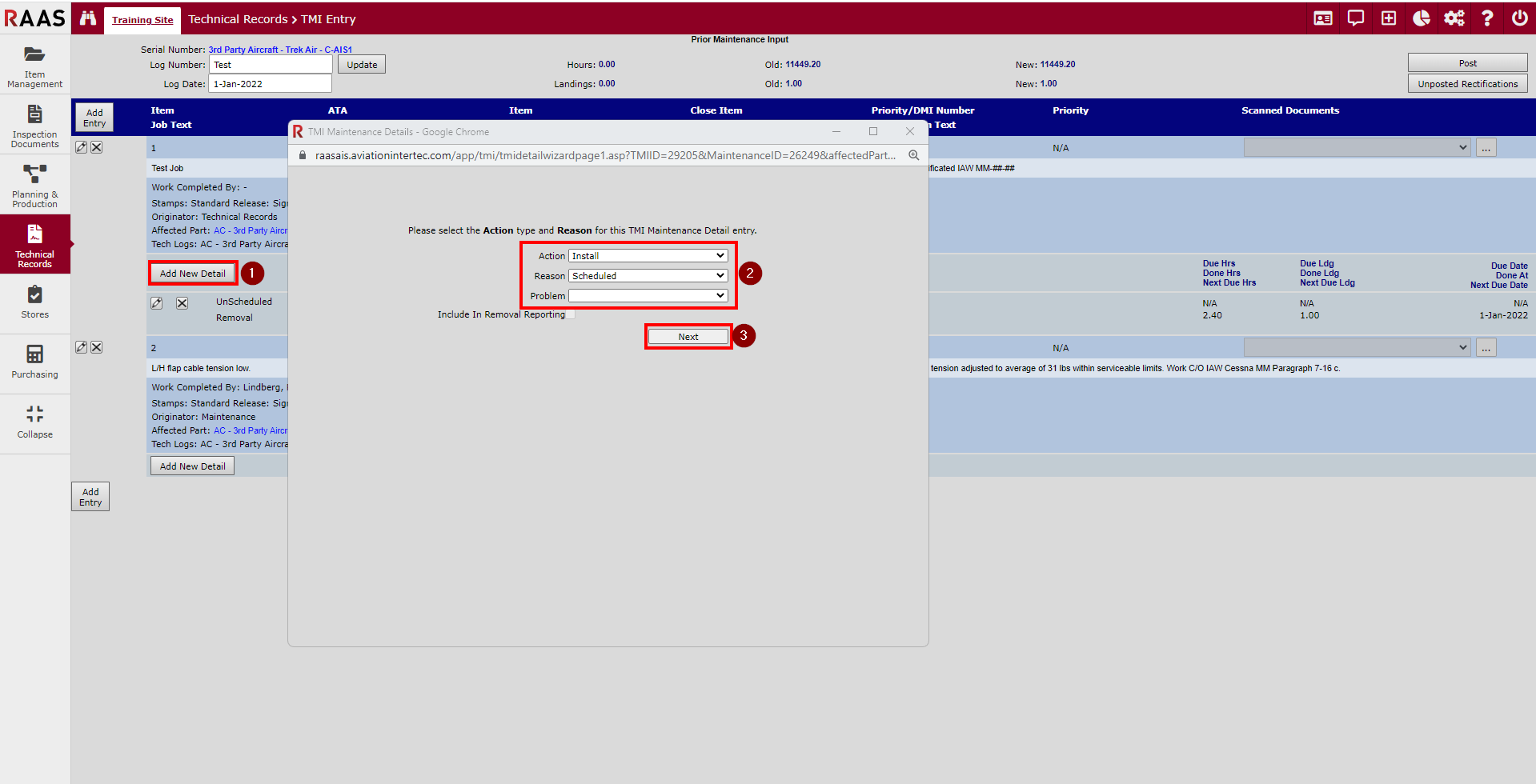
Figure 4: Action, Reason, Problem - Installation
Part for Maintenance
Select the desired Search Type, enter the search criteria and click Find.
Select the applicable Serial Number.
Click Next.
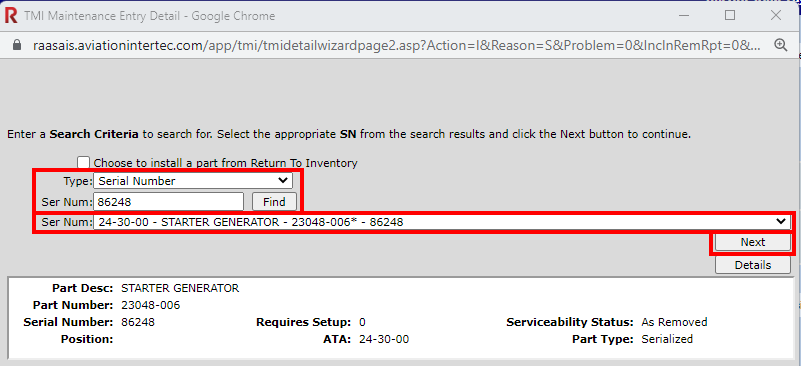
Figure 5: Selecting a Part to Install
The Details button will open the Serial Number Details window for any part verifications.
Installation on an Aircraft
The installation Serial Number will default to the Airframe.
Add a Position if applicable (can be left blank if ‘Only’).
Click Next.
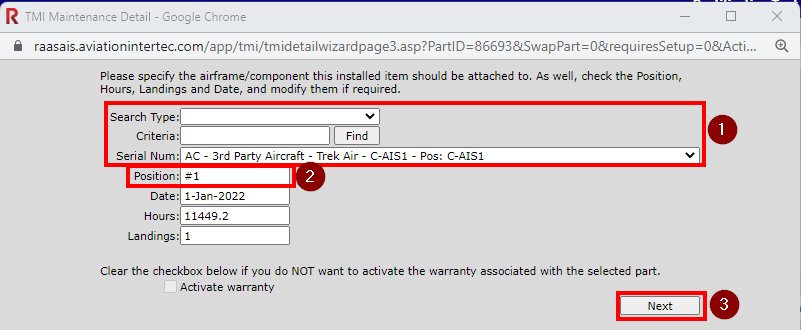
Figure 6: Installing on Aircraft
If a part being installed is part of an assembly (ie. Engine, Propeller, Landing Gear etc.), follow the steps below.
Installation on a Component
Select the desired Search Type, enter the search criteria and click Find.
Select the applicable Serial Number.
Add a Position if applicable (can be left blank if ‘Only’).
Click Next.
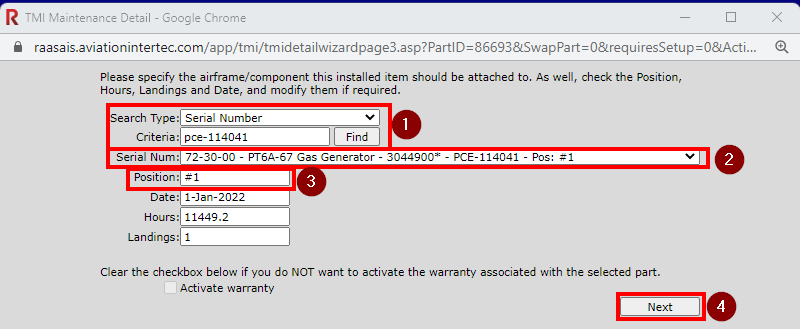
Figure 7: Installing on a Component
If the maintenance detail entry was for an Installation more details may be required (see Comply, Reset, Comply/Reset).
If the Installation does not require more details skip to TMI Maintenance Details Result.
Part Swaps
When parts are swapped on the airframe (ie. for troubleshooting) a TMI Entry can be made for the Removal of the parts and posted; then a PM Log (Prior Maintenance) can be created to Re-Install the parts with the new positions.
When parts are swapped on an assembly (ie. an engine) a TMI Entry can be made for the Removal of the parts and posted; then a PM Log can be created to Re-Install the parts on the proper assembly.
Comply, Reset, Comply/Reset
Selecting Comply for the Action on an inspection or rotable part will save the Last Done details to the Serial Number and suspend the constraint.
Selecting Reset for an inspection or part will reset the next due but will not update the Last Done information on the SN Details.
A Comply/Reset for an inspection or rotable part will save the Last Done details to the Serial Number and reset the constraint to the next due.
Inspections
When a Planned Inspection is completed it will require further Maintenance Detail depending on the type of Constraint.
Action, Reason, Problem
Constraint - Repeat: Comply/Reset
The Affected Part will tell you what type of Constraint the Inspection was raised for.
Click Add New Detail.
Action: Default Comply/Reset, Reason: Default Scheduled, Problem: none required.
Click Next.
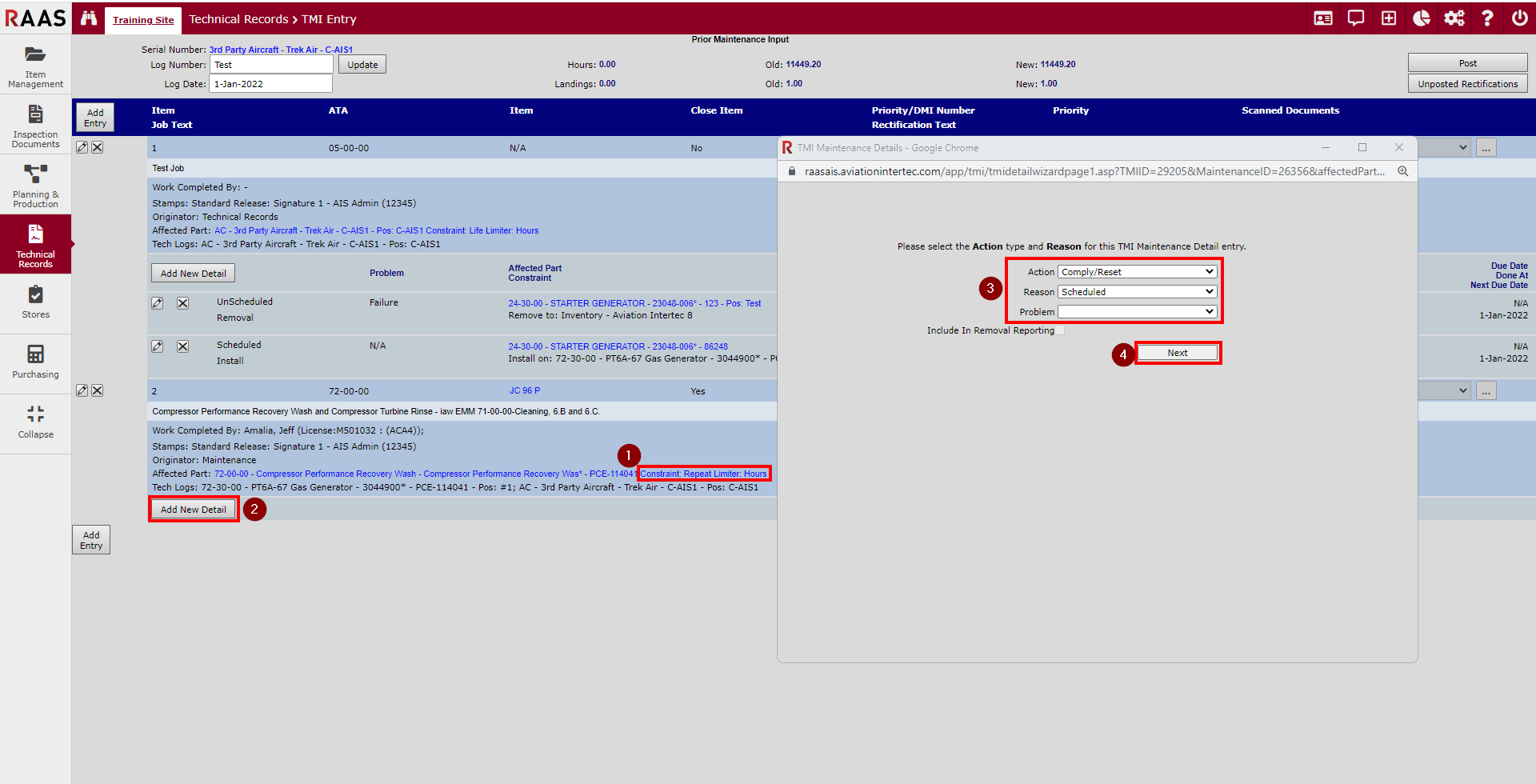
Figure 8: Action, Reason, Problem - Comply/Reset Inspection
Selecting Inspection for Comply/Reset
The Affected Part will automatically be selected in the Search Criteria window.
Verify that it matches the Affected Part detail.
Click Next.
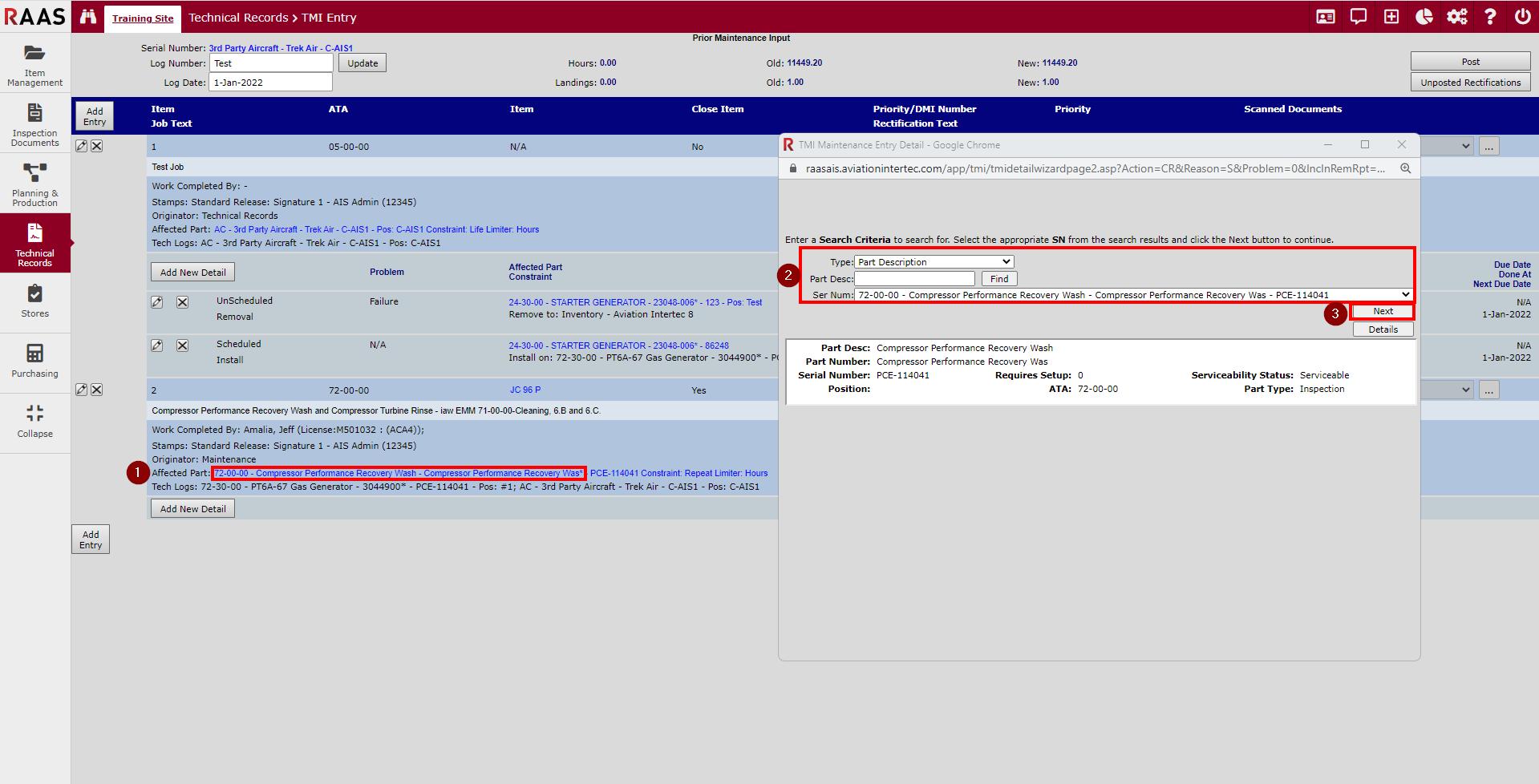
Figure 9: Selecting Inspection for Comply/Reset
Selecting Comply/Reset from Due, Done or Manual
Verify that the Constraint matches the Affected Part. Verify the Date, Hours and Landings.
Specify whether to calculate the Next Due from the From Done time, From Due time, or if you would like to input a Manual Next Due time. The default will be From Done.
Click Next.
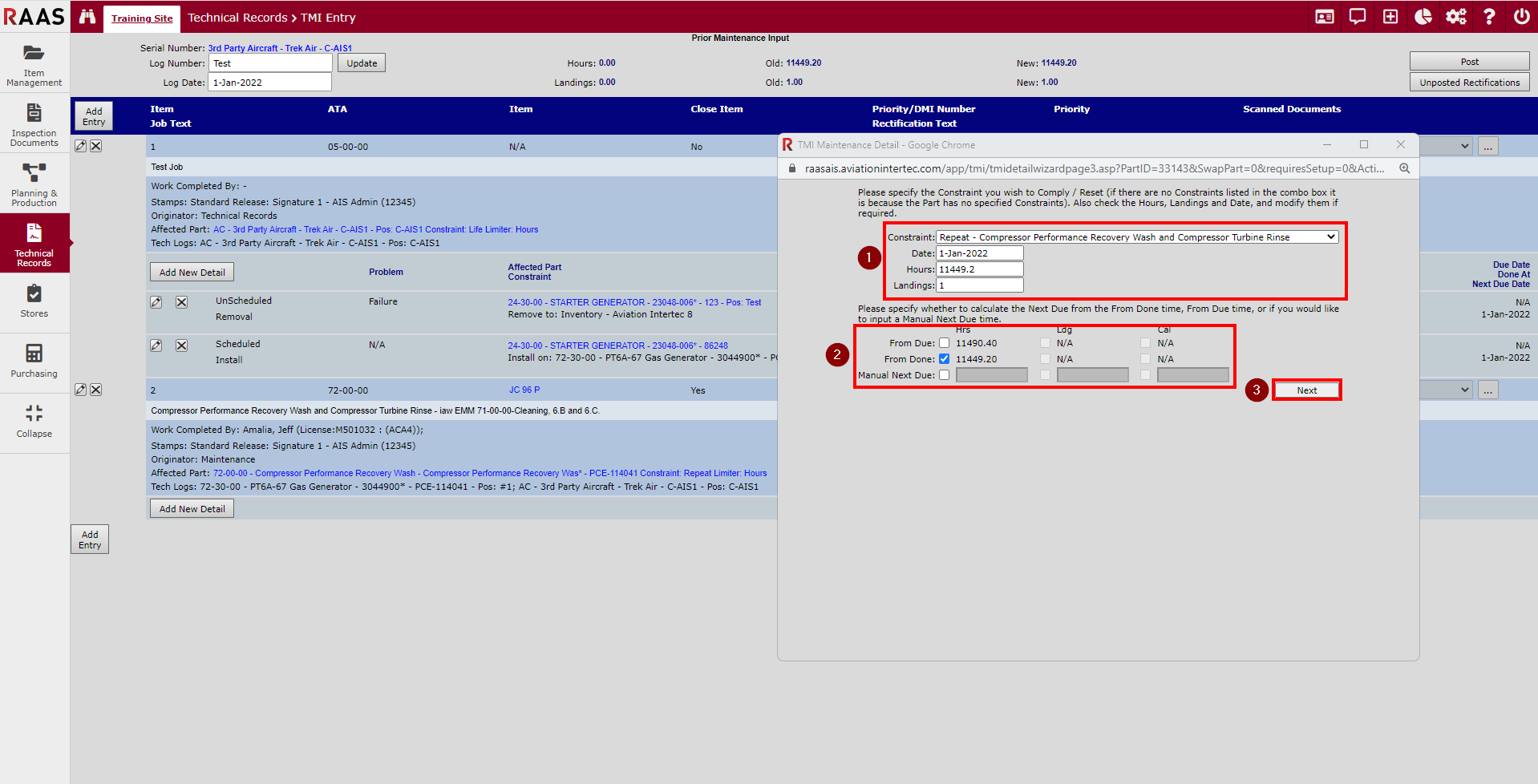
Figure 10: Selecting Comply/Reset from Due, Done or Manual Next Due
Action, Reason, Problem
Constraint - Initial: Comply
The Affected Part will tell you what type of Constraint the Inspection was raised for.
Click Add New Detail.
Action: Select Comply, Reason: Default Scheduled, Problem: none required.
Click Next.
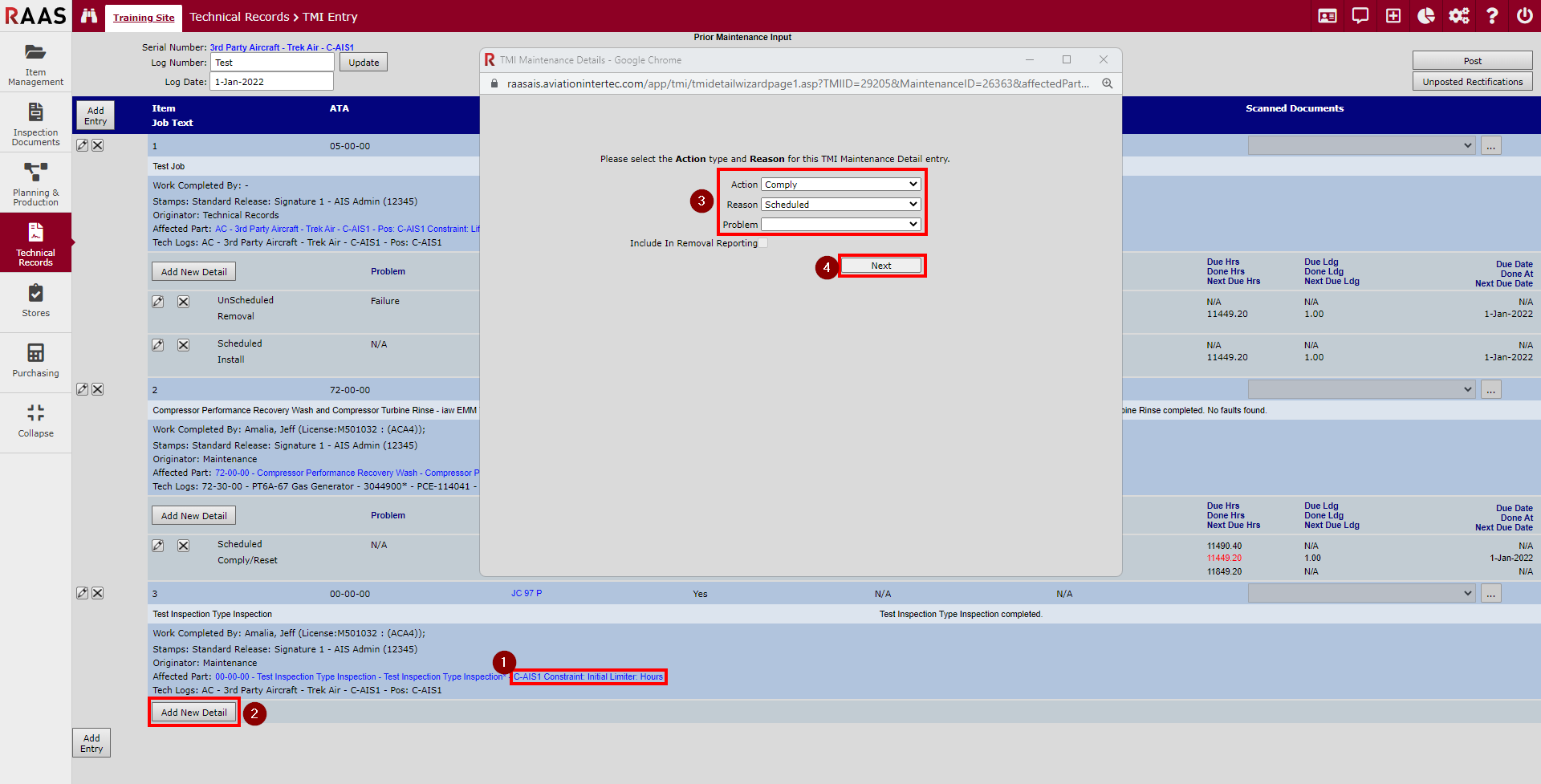
Figure 11: Action, Reason, Problem - Comply Inspection
Selecting Inspection for Comply
The Affected Part will automatically be selected in the Search Criteria window.
Verify that it matches the Affected Part detail.
Click Next.
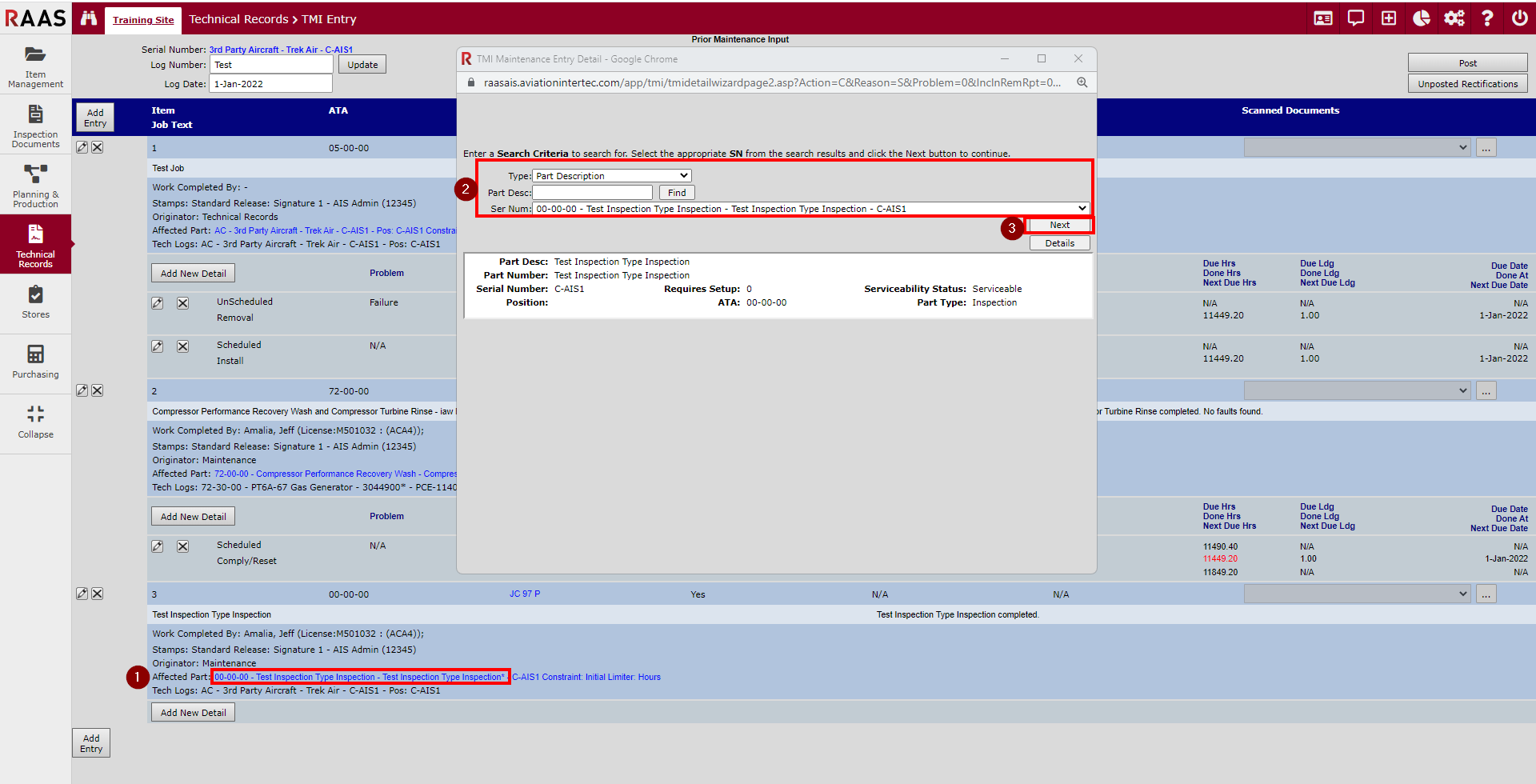
Figure 12: Selecting Inspection for Comply
Comply - Reason for Suspension
Verify that the Constraint matches the Affected Part. Verify the Date, Hours and Landings.
Reason For Suspension: must be entered.
Click Next.
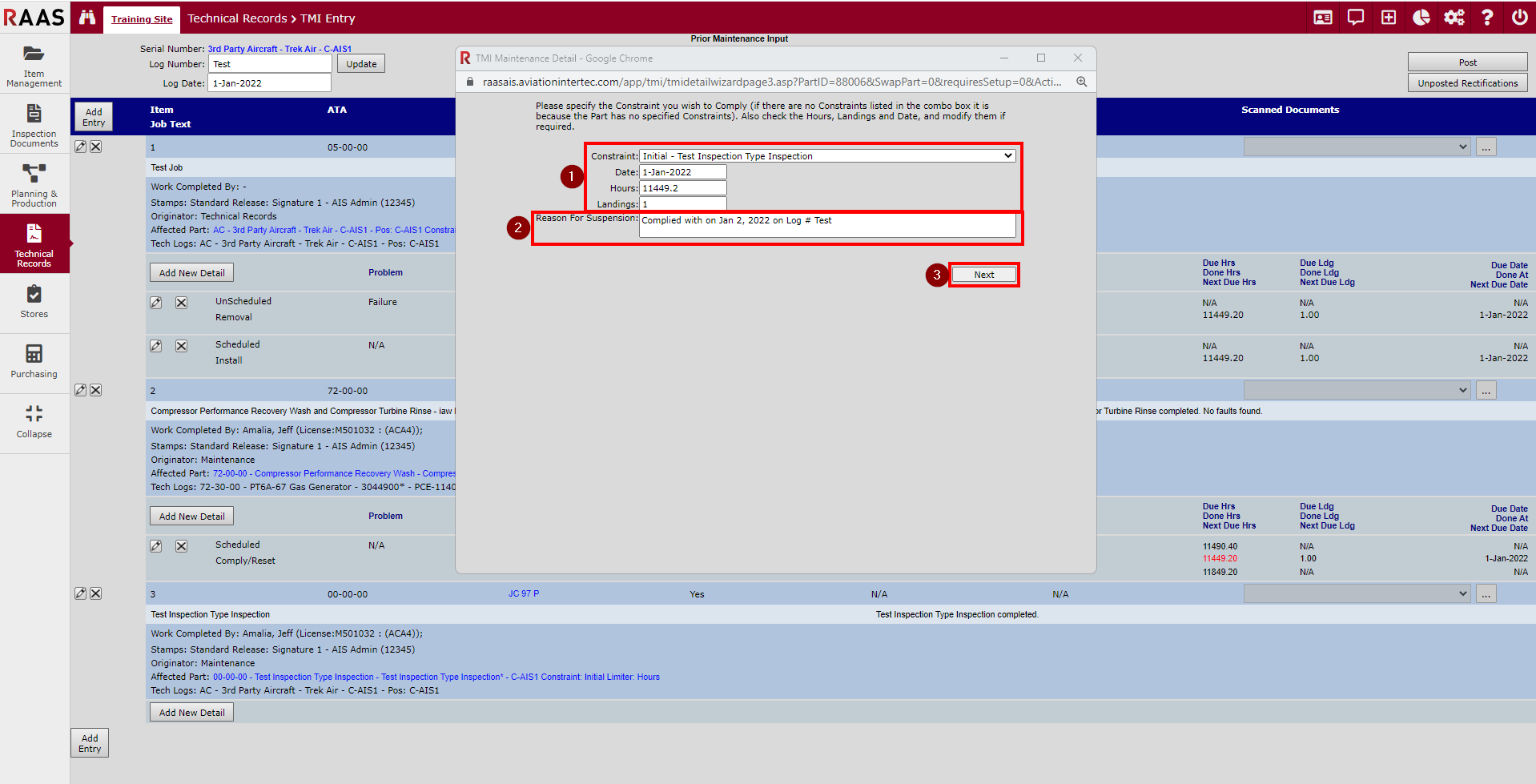
Figure 13: Comply - Reason for Suspension
When an inspection is an Initial (one-time only) and is Complied it will then be suspended with a reason and will not come due again in the future. If an inspection is an Initial to be followed by a Repeat Inspection a Trigger window will pop up (see Triggers).
Action, Reason, Problem
Constraint - Life: A Life Constraint can be treated either as a final limit - Comply (suspension) or as a Reset action.
The example below is for Reset - see also Comply above.
The Affected Part will tell you what type of Constraint the Inspection was raised for.
Click Add New Detail.
Action: Select Reset, Reason: Default Scheduled, Problem: none required.
Click Next.
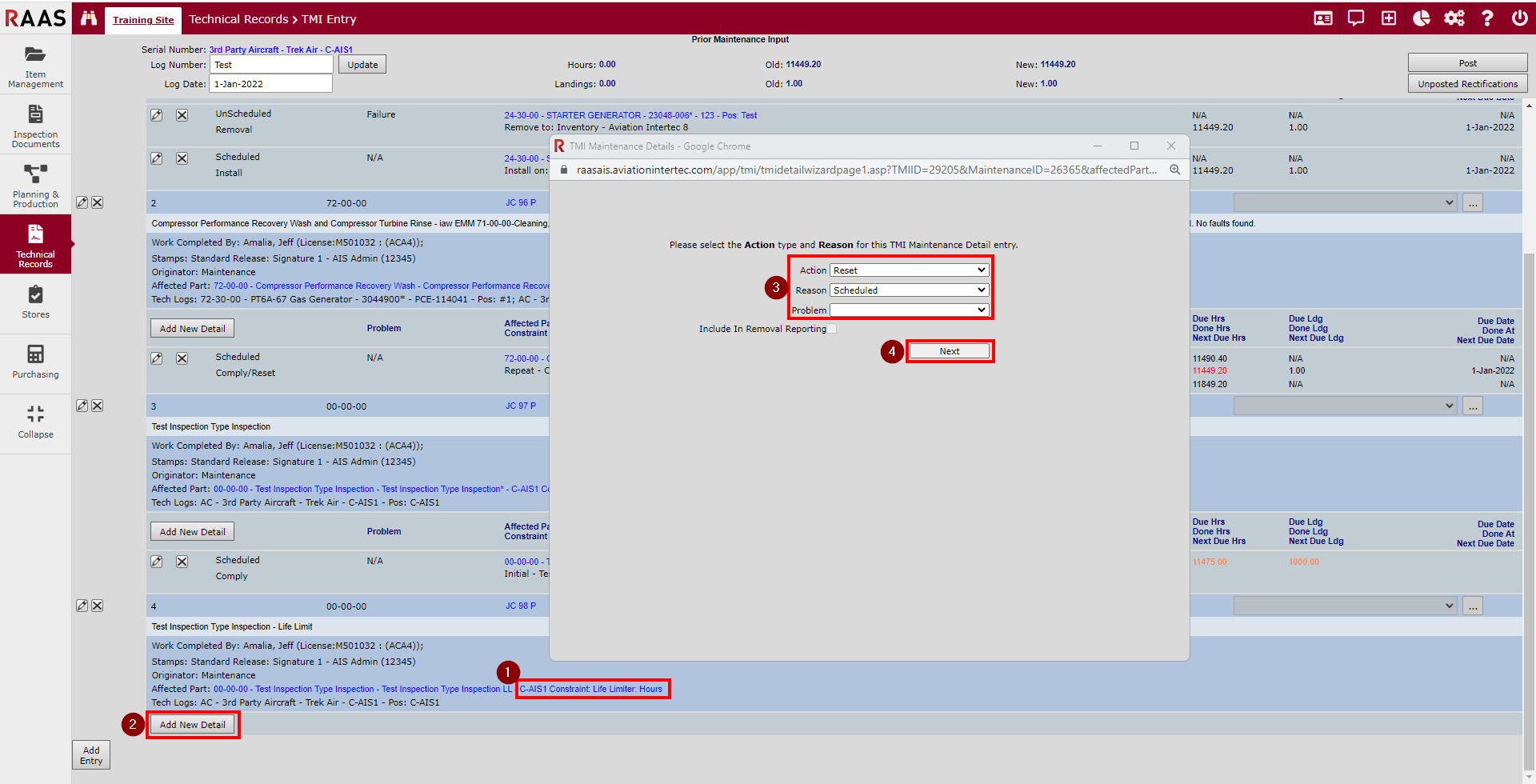
Figure 14: Action, Reason, Problem - Reset Inspection
Selecting Inspection for Reset
The Affected Part will automatically be selected in the Search Criteria window.
Verify that it matches the Affected Part detail.
Click Next.
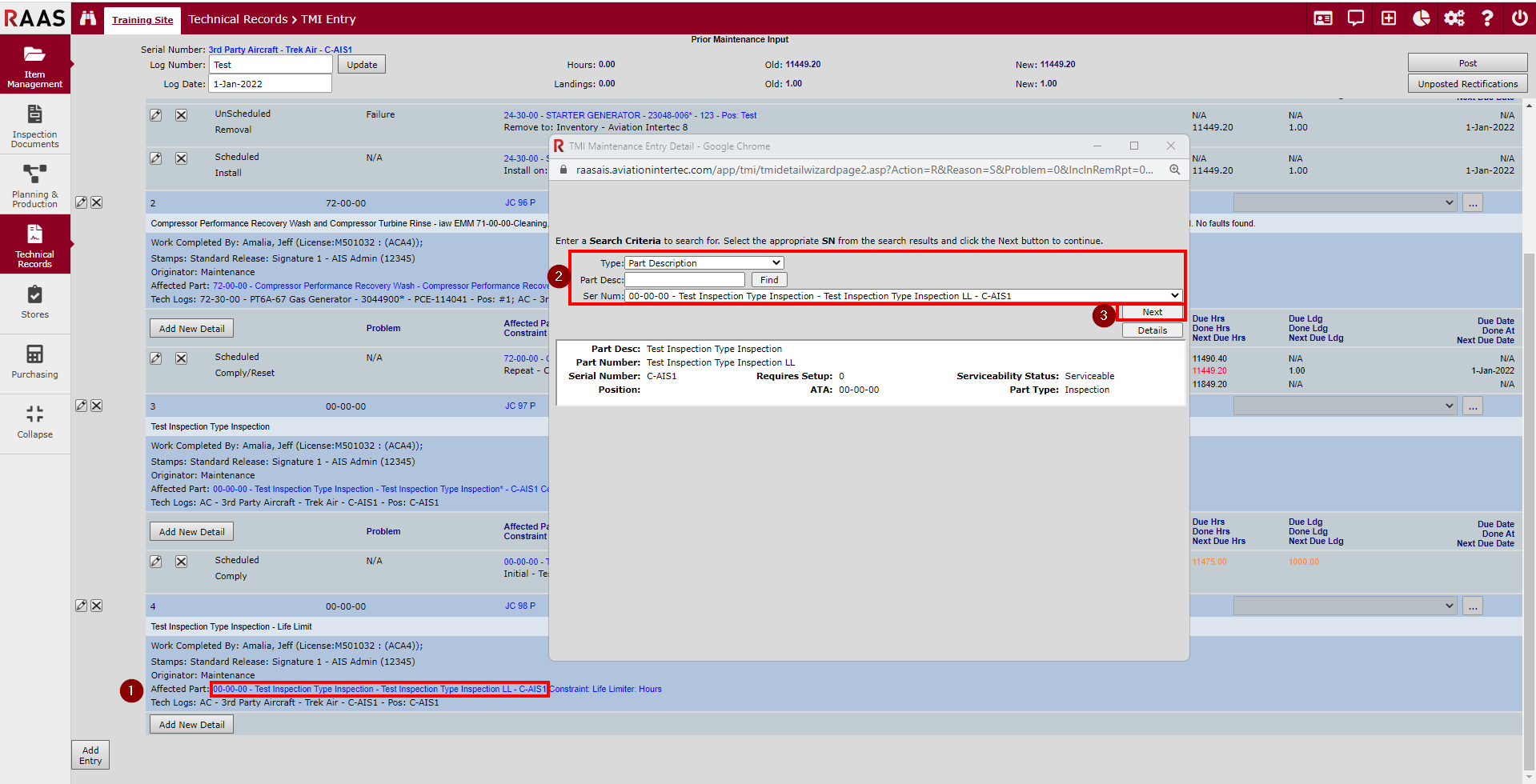
Figure 15: Selecting Inspection for Reset
Reset - from Due or Done
Verify that the Constraint matches the Affected Part. Verify the Date, Hours and Landings.
Specify whether to calculate the Next Due from the From Done time, From Due time, or if you would like to input a Manual Next Due time. The default will be From Done.
Click Next.
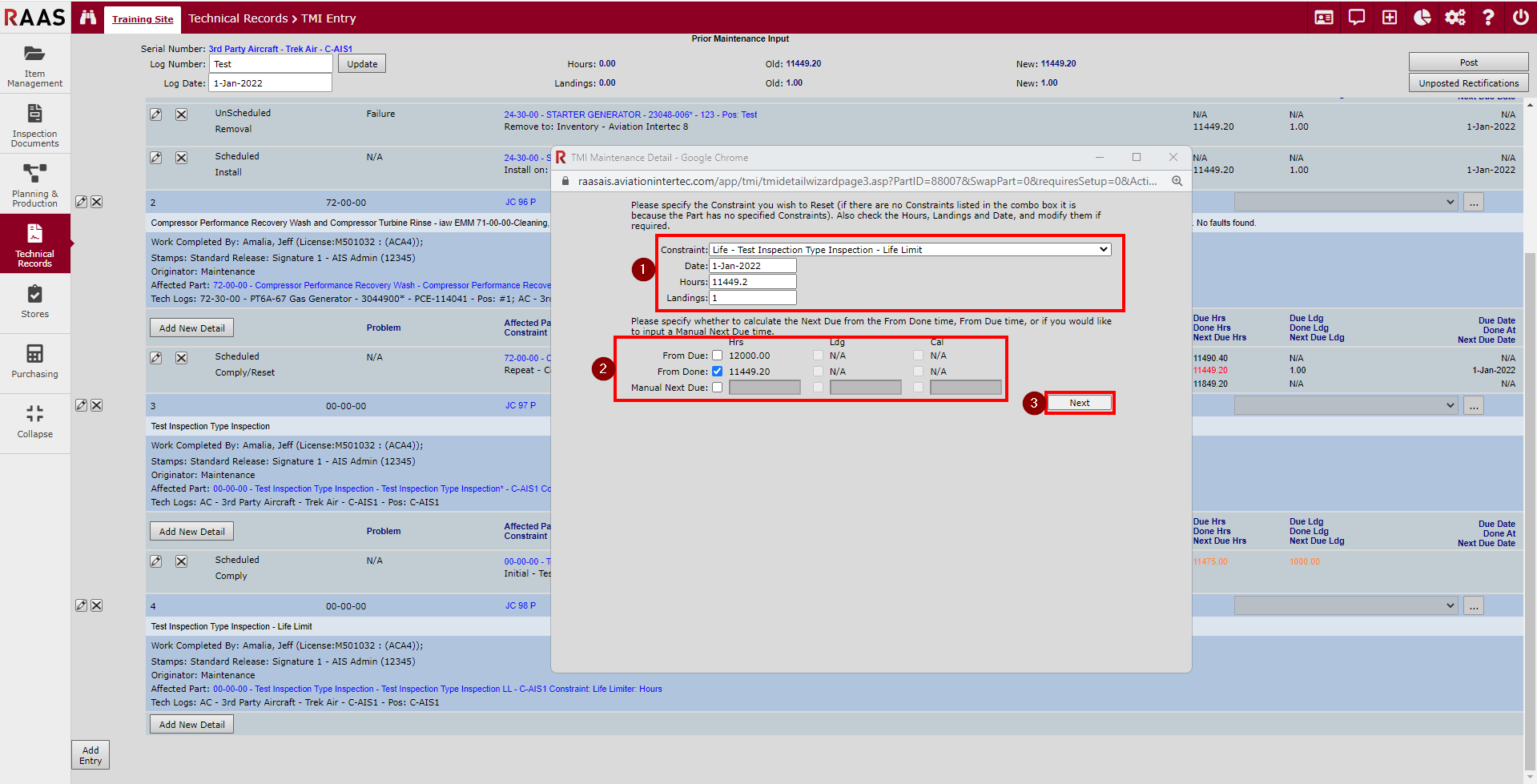
Figure 16: Reset - from Due or Done
TMI Maintenance Details Result
When all entries for the TMI log sheet have been added, click the Post button to allow the entry to be recorded in RAAS.
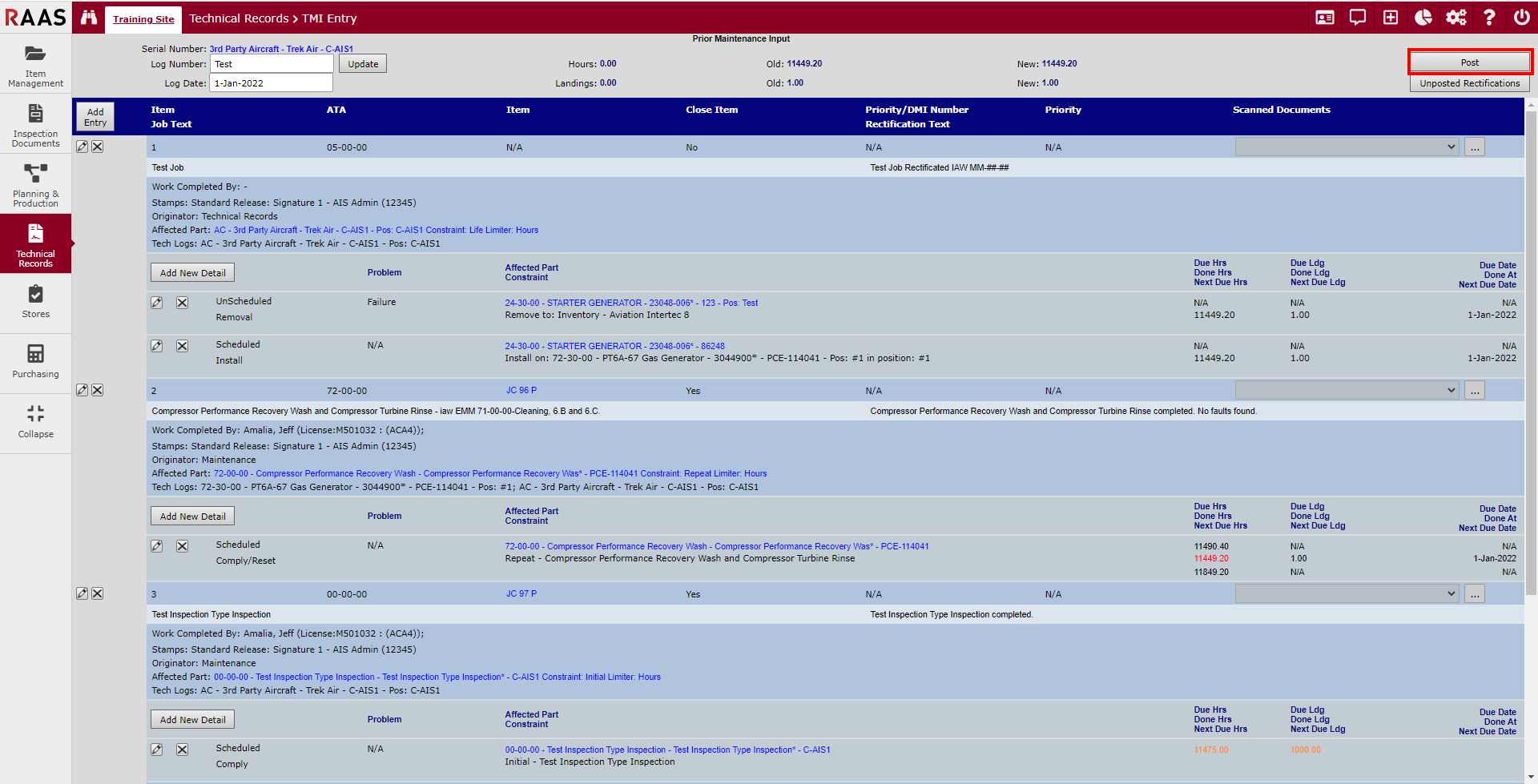
Figure 17: Posting TMI Entry
Triggers
RAAS employs an automation feature called Triggers to aid tech record entry. Completion of a TMI action having an associated trigger causes a popup window to appear.
Message triggers show text reminders, like a kind of electronic post-it note.
Action triggers automate the creation of one additional action based on the completion of the first action.
Cascading Non-Interactive Triggers are used in managing phased inspections.
Action Trigger Addition
Click the + button in the top pane of the popup window.
If applicable, supply user credentials for those triggers requiring elevated permissions.
Click the applicable follow-up action in the lower pane labelled Available Serial Numbers.
Click the Add button.
Click the Next button to dismiss the popup window.
Click the pencil icon belonging to the automatically added action, indicated with a red T; step through the detail editor raised to confirm the addition.
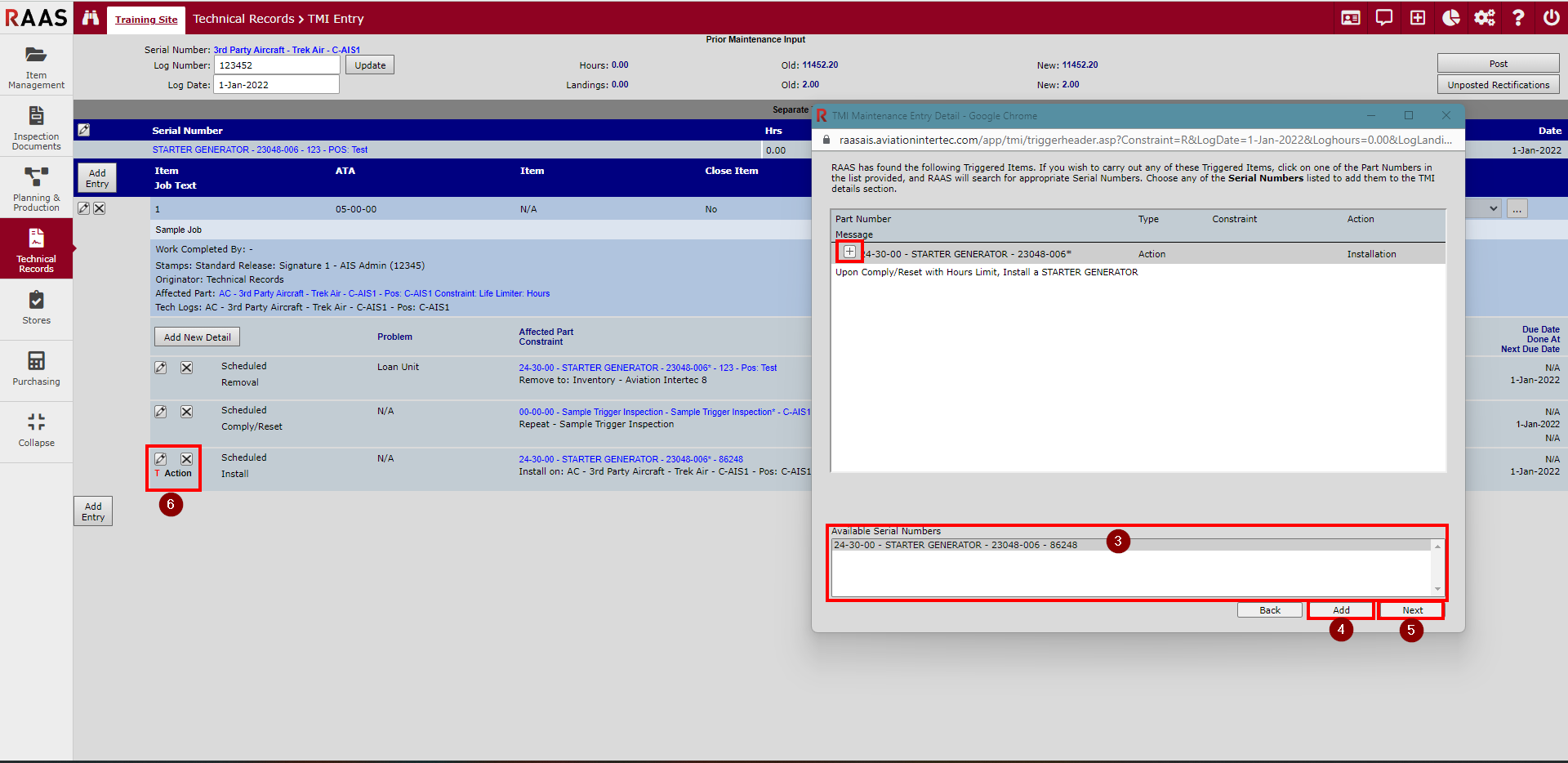
Figure 18: Selecting an Installation Component from a Trigger