CALIBRATED TOOL TRACKING
Calibrated Tools are loaded in the same way as non-calibrated tools, but with extra considerations, as these items require an expiry or ‘Next Due’ to be tracked. The process for entry of these items is as follows:
Locate or create the required Part Description details.
Item Type would be Tool
Locate or create the required Part Number details.
Inventory Type would be TOOL
Add a new Serial Number and confirm:
Position (shelf)
Installation Details (typically Tool Crib)
Constraint requirements (last done/next due)
Save Serial Number details.
Select the Trace and edit the Initialize trace.
Update the following values if required:
Trace
Receipt Price
Receipt Date
Serviceability Status
Owner/Vendor
Other fields as operationally relevant
Enter a reason for modification and effective date.
Save.
Additional Configuration
In addition to the above process, Calibrated Tools require additional configuration via one (or multiple) of the following processes:
Shelf Expiry Configuration
Enable the Track Shelf Life flag on the Part Number details
Edit the Trace Details and add an expiry date in the Has Shelf Life box
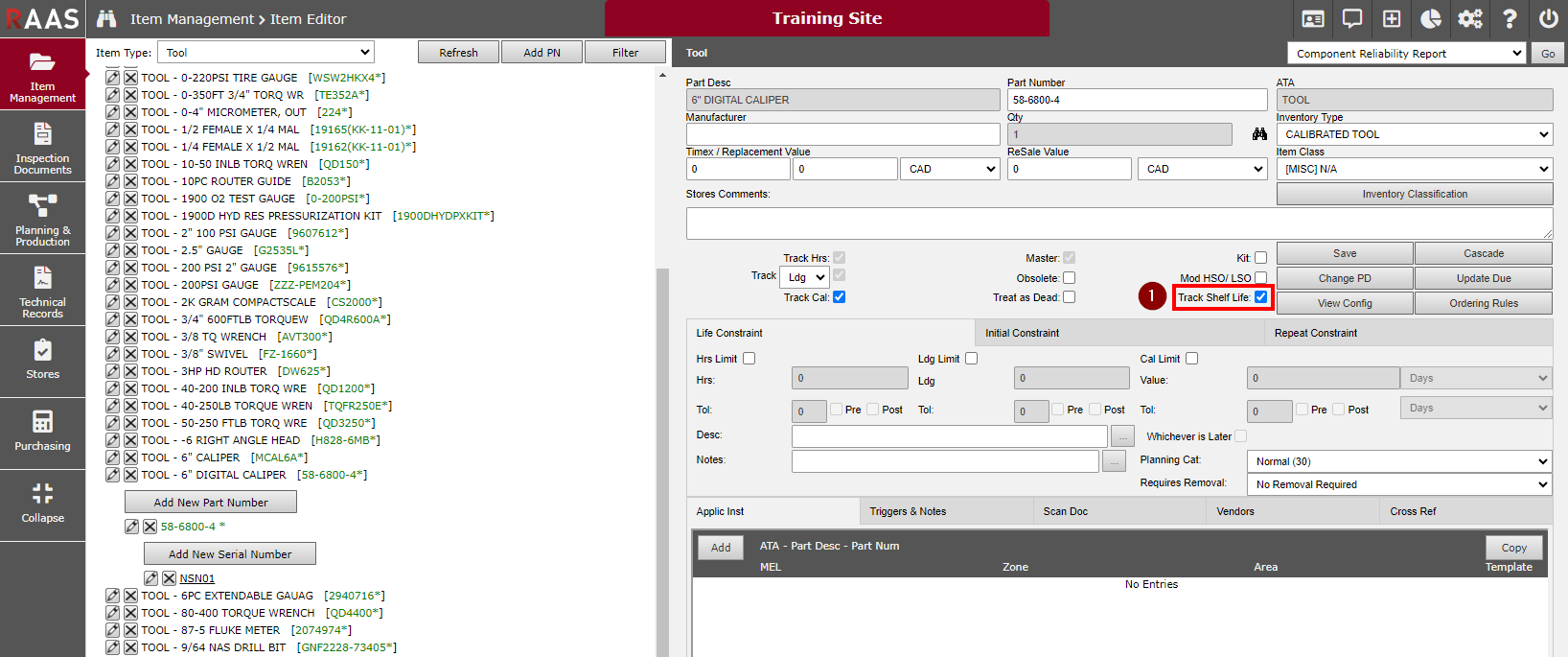
Figure 1: Track Shelf Life
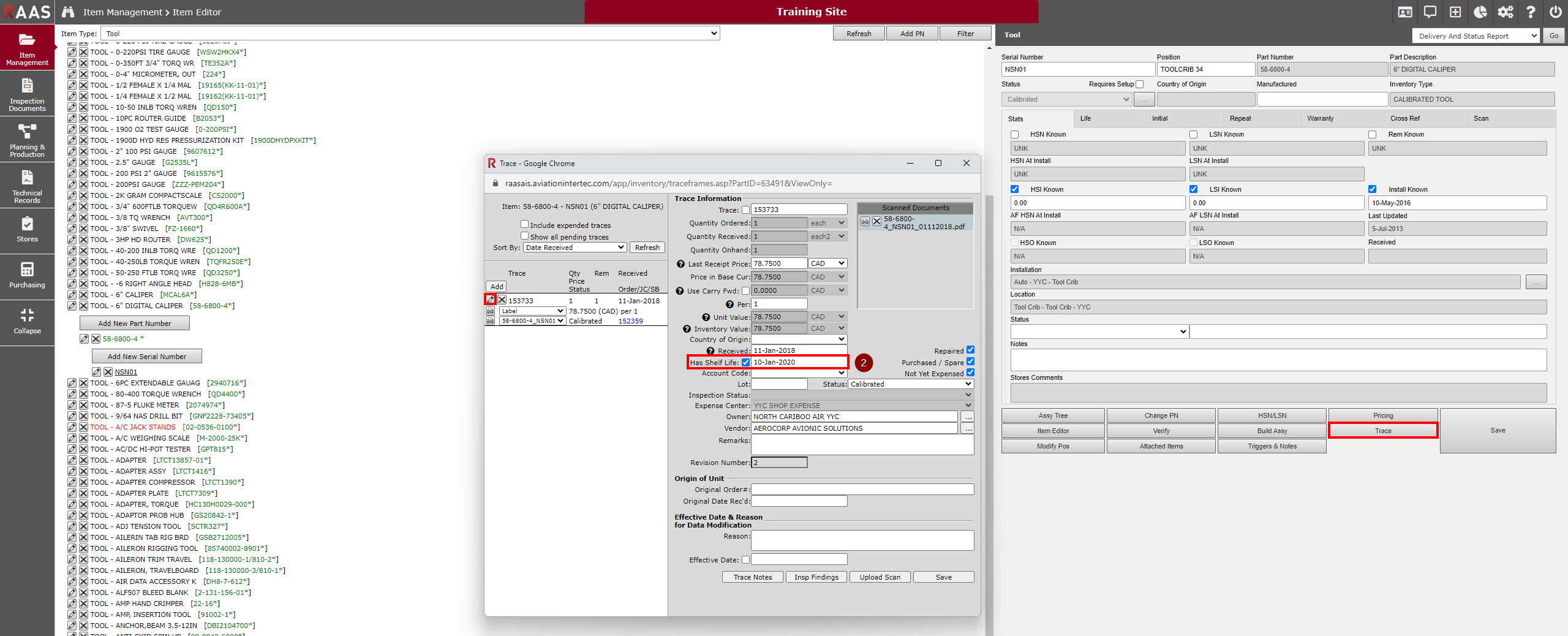
Figure 2: Trace Details: Enter Expiry Date
Constraint Configuration
Edit the Part Number details to track a Repeat Constraint requirement to ‘Calibrate Tool IAW ____’
Edit the Serial Number details to track a Next Due on the tool calibration requirement
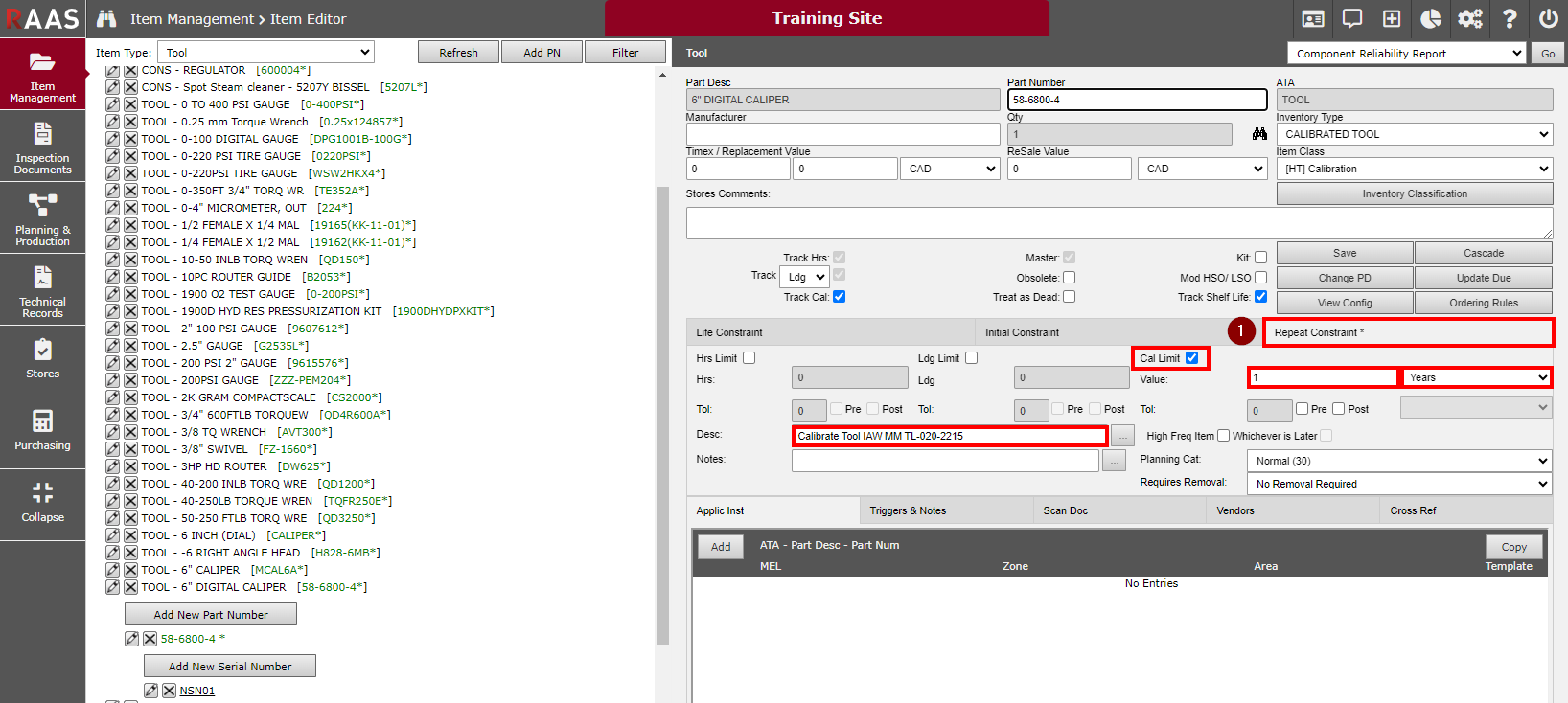
Figure 3: Set Up Repeat Constraint
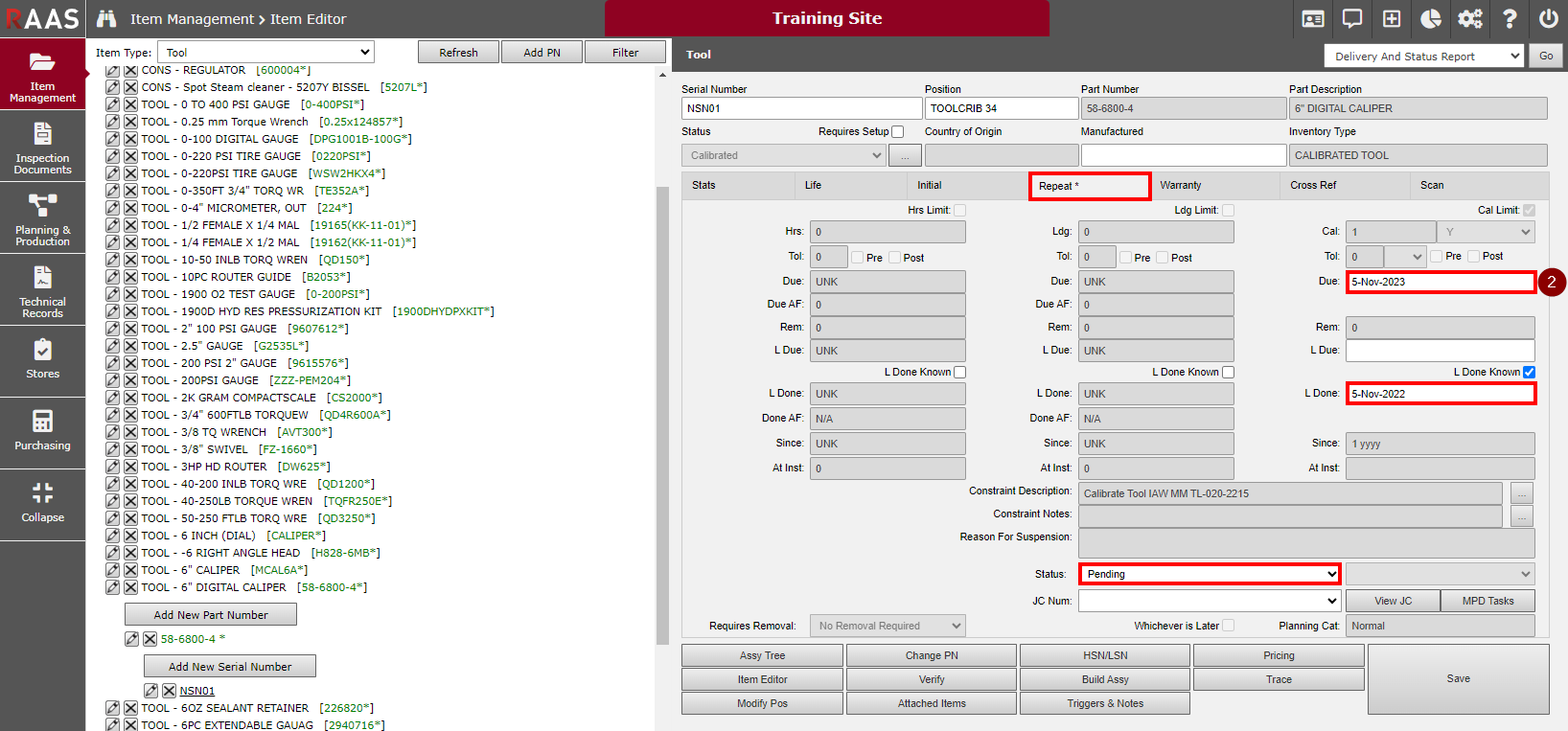
Figure 4: Track Next Due
Material Inspection Configuration
Edit the Part Description details to flag Requires Material Inspection.
Edit the Part Description details to flag Send Notification on Receipt.
Employees wishing to be notified must have “Receipt Report” flag on under Options>Employee Information with a valid Email (Bus).
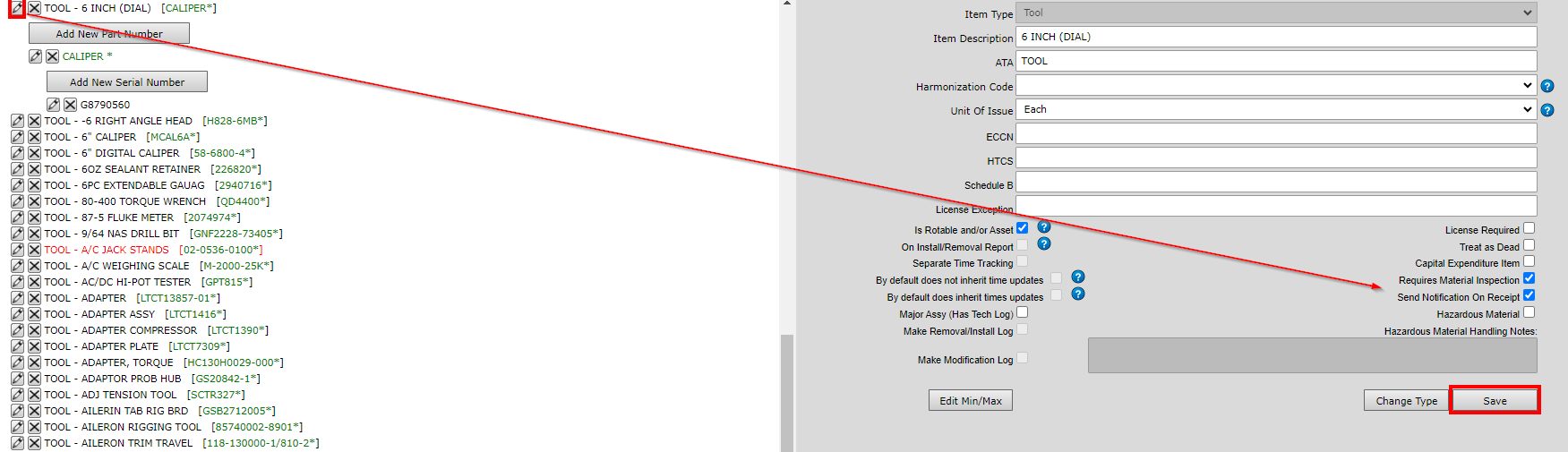
Figure 5: Material Inspection
Tracking
Shelf Expiry Configuration: Allows Tools due for calibration can be tracked using the Expired Parts List by selecting Location: Tool Crib and Inventory Type: Tool.
Constraint Configuration: Allows Tools due for calibration to be tracked using the Maintenance Forecast. Further, this can be set up as a Maintenance Forecast Profile, allowing for automated reporting on Tool Crib due dates on a regular basis.
Material Inspection Configuration: Allows specific employees to be notified when a Tool is received from calibration that requires a Material Inspection before allowing the tool to be used.